What is a Quality Culture? (and 7 Tips for Creating One)
.png?width=800&height=400&name=What%20is%20a%20Quality%20Culture_%20(and%207%20Tips%20for%20Creating%20One).png)
In the medical device industry, the word quality can mean different things to different people. To some, meeting compliance requirements is quality. To others, quality is improving the life of a patient who uses their device.
While both statements are true, only one is reflective of a true quality culture. There’s a difference between meeting quality regulatory standards and fostering a quality culture in your company, and this guide will walk you through everything you need to know about it.
Refining and improving culture is a goal every medical device company should have on its agenda, as doing so pays off in many ways throughout your project lifecycle. Let’s start by examining exactly what I mean by “quality culture.”
What is a Quality Culture?
A quality culture is an environment where team members genuinely care about the quality of their work, and make decisions based on achieving that level of quality.
You know you have a quality culture when there is a recognition amongst all levels of a company that quality should be achieved for its own sake, and not just to meet regulatory approval.
There are a lot of companies out there with their quality policy printed on the office walls for all to see. Can their employees recite the policy? Sure, probably. But do they care? Can they truly relate to it, or are they just committing it to memory as a chore? There’s a big difference, and it shows.
At the end of the day, everything you’re doing should be about the well-being of the end user and patients who will be helped by the products you’re making.
A true quality culture is, of course, fundamental to making a product that’s safe and effective in order to improve patient lives. If your team has that in mind at all times, odds are you already have a good quality culture.
If not, the issue isn’t that your company doesn’t care about its end users - the quality culture just hasn’t been fully fostered, leaving you with a great opportunity to make improvements that will trickle out into every aspect of your business and raise the standard of everything that you do.
7 Tips For Creating a Quality Culture
Below you’ll find our 7 top tips for creating the best possible quality culture in your company.
1. Define and Outline Company Values
If you want to raise the standard of your quality culture or establish a new one, the first thing you need to do is make sure that your company values are clearly defined. Think about the values your company already has in place - do these speak to quality? Are these values ones that you want? Is there room for improvement?
As we know through working in the medical device industry, it pays off to adopt a methodical approach. The process behind your company culture should be no different. Carefully strategize how to go about fostering your quality culture now in order to set the example for your team, and the natural force behind it will take hold.
One effective way to do this is to encourage employees to adopt a mindset that every product they work on, regardless of which stage they touch it, eventually will be used on a family member. This approach establishes a holistic nature to quality culture that will impact all aspects of your business - from product development all the way to commercialization practices.
Again, focus on the patient here when you’re thinking about your values. Once you figure out how you will foster your quality culture, brainstorm with your team about the goals you’re aiming to achieve with your project and go from there.
Final note here - I often see companies in the research stage approach quality culture as a future initiative to tackle down the road, and that’s not advisable in my opinion.
You may feel that you don’t need a defined quality culture until further down the line, but by that stage, your company will have formed certain processes and habits that will be more difficult to break. To apply this in a practical sense, consider root cause analysis--would you rather address a potential problem in its infancy phase, or wait until it’s become a systemic issue?
An overhaul consumes more time and resources than getting it right in an early stage, so it’s imperative to operate with quality in mind from the onset.
2. Train Employees in Quality Culture
Training is a worthwhile investment that pays dividends over the course of a company’s development. Adept teams are formed by taking part in various aspects of training, including activities that reinforce the values of quality culture within their company.
An unfortunate fact about corporate training is that it’s often ineffective. Research shows that 90% of the information we learn at any given time is actually forgotten after one month! Given the cost of external training, this statistic presents a major cause for concern.
In my opinion, part of this is due to the mindset of those being trained, and I don’t mean that as a criticism.
People can undergo all the training in the world, but they need to have an understanding of how their personal training will be beneficial and actually add value, both to them as an individual and to the company.
Training is often mandated through regulatory requirements or disciplinary courses of action following an audit or inspection, but shouldn’t be adhered to as a checkbox activity. Training is an opportunity for teams to develop new skills that can be used to improve upon products and processes.
One issue I see with training is that there’s not always a clear way to measure its efficacy - a person may receive a slip of paper acknowledging certification, but this doesn’t mean much if that person doesn’t retain the information needed to effectively function.
The way to navigate this is to here is to adopt a quality mindset for improvement.
3. Pursue Quality Instead of Chasing Compliance
Many companies find compliance to be a burdensome process, but true quality and compliance simply go hand in hand.
Here’s the thing - just because you’re in compliance doesn’t mean you’re producing a quality product. I can think of fast food restaurants that, on paper, are compliant with regulations, but don’t produce quality tasting meals.
Considering the needs of internal and external stakeholders, which includes patients, will result in such a high quality that compliance becomes a natural byproduct.
I see a lot of companies building a quality system simply as a means to satisfying regulatory requirements, but this is another missed opportunity to build out one’s quality culture and reap the long-term rewards.
Companies that only focus on compliance tend to view quality culture as a task for the Quality department, but it must be approached as a company-wide effort. Quality teams are often viewed as separate from the rest of the organization because they often assume the authority to inspect work, request do-overs, and in doing so, assume the responsibility for halting progress momentum.
Obviously, this isn’t a fair way to view Quality staff members, and it’s a mindset you should be vigilant in correcting if you come across it within your own company. Your whole organization should embrace a quality mindset in everything you do, and every interaction across departments.
I’ve found that when I explain to external stakeholders what the parts of a medical device are actually used for, I can evoke an emotional response and investment in the product that leads to increased quality. By understanding the purpose or the need it serves, there's a new sense of pride in the work that is produced.
People want to feel like they're doing something that matters, and if your team is responsible for developing and producing medical devices, everyone involved is doing something that matters - you just need to make sure they understand their role in the process in order for them to feel a certain way about it.
When quality is truly embraced in all facets of a company, you have a better product and fewer headwinds, it’s as simple as that.
4. Implement Document Control Early On
Document control refers to the policies and procedures that should be in place to ensure that there is organizational accountability for records and other data.
Document control is fundamental to the success of all medical device companies. Done right, this allows for scaling and makes quality repeatable. From a regulatory sense, it’s your way of proving your documentation is following necessary requirements for compliance.
Like quality culture itself, I strongly recommend companies implement their document controls as early as possible.
Early document control can often catch errors and faults that can then be corrected while still in the early stages, making it easier to keep track of things.
Let me give you an example of the kind of benefits this can bring - let’s say you’re in the research stage of your project, and you send away design outputs for prototype manufacturing. A documentation error during this process will delay your project and can waste significant capital... money you could have used to budget for a more stringent document management system.
Having a good quality management system (QMS) in place can make document control a lot easier. This is one of the reasons why we created Greenlight Guru, to serve as an electronic QMS that addresses and solves pain points in processes like document control, an area where it’s much too easy for documents to get lost in paper-based systems or applications not designed to manage the specific data set required for medical devices.
Each document can be monitored for approval status with full traceability across the most recent versions for simple implementation and management as you scale.
5. Communicate Clearly With Regulators
It’s important to align yourself with regulators as much as possible. If you’re not planning and building systems according to quality standards, your risk of noncompliance is high and will eventually be uncovered at some point in the process.
Regulators are essentially looking for risk in your operations, which is one of many reasons why risk management and quality management are so closely interconnected.
When working alongside regulatory officials during an audit or inspection, you should make sure their visits are as seamless as possible. This can be practiced and perfected with internal audits amongst all team members involved in this process. You should always be ready at a moment’s notice to produce any proof of record or procedure.
People tend to get nervous when an audit or inspection is coming up, but this comes down to how prepared they are themselves. Regulators are not the enemy - they’re simply looking out for the well-being of your end users.
In fact, I encourage you to contact regulators when you're unsure of something. While regulators can't act as consultants to device companies, sometimes they can offer valuable feedback on things like your validation testing plans, for example, or point you toward helpful resources.
It can be tempting to use internal terminology during audits or inspections, but this can create confusion and miscommunication with the FDA, potentially even resulting in a 483 observation response, leading to major delays and costs.
Follow regulation terminology from an early stage and get into the habit of doing it - that way it becomes second nature, both within your organization and with regulators, to avoid any confusion during an audit or inspection.
Regulatory changes are constant in the medical device industry and internal management of those changes takes teams away from focusing on innovation. Greenlight Guru takes the regulatory burden off companies with its medical device-specific QMS software that is continually updated to comply with the latest regulations, including ISO, FDA, and EU MDR requirements.
By making all of your processes universally understood and straightforward to regulators, you’ll earn a considerable amount of time back to use with focusing on producing quality devices that will improve the lives of your patients.
6. Seek End-User Feedback
We've already touched on a critical point of your quality culture involving ensuring at all stages that your product will have the best possible impact on the lives of your patients.
A great way to enhance your quality culture, while also ensuring your product meets quality standards, is by soliciting end-user feedback. This feedback is invaluable to your process and can help you catch design flaws that even your most critical engineers may have missed. While most companies seek this feedback well into the later stages of the project lifecycle, there are potential benefits to be gained if done properly in earlier stages
You can solicit feedback through focus groups and surveys at any time in your lifecycle journey, and doing so will have a positive effect on your quality culture.
When done effectively, you should seek feedback at multiple stages for the best possible results. Ideally, you’ll have already placed built-in mechanisms during the design and development process to facilitate this. You’ll also want to do this at various intervals once the product is in the marketplace to monitor its ongoing progress
This type of proactive approach is prioritized by regulatory bodies and is one I frequently recommend companies take. This can reduce quality issues and create opportunities for being proactive, rather than feeling forced to take a reactive action, such as CAPA.
This falls under post market surveillance (PMS), and is often a regulatory requirement covered under EU MDR, FDA 21 CFR Part 820, and ISO 134585:2016. You’re typically obligated to monitor the performance of your product on the market because clinical trials are not required for every company and even when they are, you can never fully replicate real market conditions.
Whether you’re required to implement PMS activities or not, there’s a lot of value in doing so. Keeping an eye on the performance of your product and the processes around it protect end users and helps inform your future product development decisions.
7. Use a Right-sized QMS
Your quality culture hinges on the efficacy of the system you use to manage your quality - it’s essential to have the right foundation, infrastructure, and tools to oversee and maintain that quality culture, and the way you set up and manage that operation is both important and bespoke.
There’s no set way to right-size your QMS, and typically there are two extremes.
On one hand, you have companies using a QMS that is far too light to cover every one of their procedures. In these instances, a company may have had an idea for a device but drastically underestimated the regulatory requirements involved.
A sparse QMS setup means ambiguous procedures and documents that result in routine tasks being done in different ways by different people.
On the other hand, you may have the overly-burdensome and complex QMS that delays processes and creates more work than necessary for the type of company using it. Startups can often comprise of people coming from bigger companies who assume they will need the same level of vast capabilities, when in reality that isn’t the case.
While it’s best to be prepared early on when it comes to documentation, going overboard too soon can create unnecessary costs and hurdles for companies along the pathway to market. Just because you’re in compliance with regulatory standards doesn’t make you immune from all potential audit findings. Companies can avoid a common pitfall by always adhering to their documented SOPs and requirements.
A startup with four people doesn’t need a massive QMS straight away - because they can all easily work in the same room, they can get away with a light QMS in a way that wouldn’t work for a startup of 20 people, and so on.
The main focus for early-stage companies is to get their product through the regulatory submission process. In order to establish the first phase of your QMS, there are some essential processes that must be implemented from the onset:
- Document control and records management
- Design controls
- Risk management
- Supplier management
Those are just the basics. If you’re not sure if you need anything else, you can always schedule a consultation with our QMS experts at Greenlight Guru and we can walk you through it.
Greenlight Guru was specifically designed to seamlessly manage your documents, design controls, risk, and supplier management, allowing your team to work in real-time with no paperwork or lost documents. The purpose-built QMS software is used by companies of all sizes, and our procedural templates and controls are certified and have been audit-tested and used by medical device companies around the world.
Your QMS should be “under construction” at all times, growing as your company scales. It’s an evolutionary process - you want to start off at the right size and go from there. Internal audits can help determine the size of your initial QMS, and they have the side benefit of keeping you more prepared for regulatory audits and inspections.
Whichever quality management system you select, make sure you know how it works before integrating it - if it’s a digital system, request a demo, speak to the designers, and so on. You can learn more about the Greenlight Guru QMS here.
Final Thoughts
The road to establishing a true quality culture isn't always easy, but there's no better way to create a solid product that will be valued by all parties.
In fact, in my experience, when a VC firm sees that a startup firm is planning its quality approach long-term, they tend to place a higher valuation on that company.
Why? Because it gives them the impression that your company has the potential to succeed and grow over time. The best part is, with a true quality culture, that impression is probably accurate.
Fostering a true quality culture puts you in a strong position with regulators, VCs, and end users. It’s a very worthwhile pursuit for all medical device companies, no matter what stage they’re in.
By now, this guide will have given you everything you need to get started on improving your quality culture and embarking on a new stage in your journey as a medical device developer.
Looking for a quality management solution to help you bring safer medical devices to market faster with less risk? Click here to take a quick tour of Greenlight Guru's Medical Device QMS software →
Jon Speer is a medical device expert with over 20 years of industry experience. Jon knows the best medical device companies in the world use quality as an accelerator. That's why he created Greenlight Guru to help companies move beyond compliance to True Quality.
Related Posts
[VIDEO] How to build a QMS using the best people, processes & technology (S.M.A.R.T Methodology)
An Introduction to FDA 21 CFR Part 11
What it Means to be Focused on Quality vs. Compliance
Get your free resource
Quality Culture Flowchart
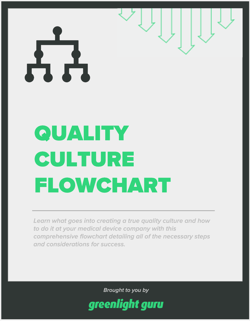