Let The Document Tell The Story: Document Management Best Practices
Good stories follow a 3-act structure:
- Act 1: Set up
- Act 2: Conflict
- Act 3: Resolution
“Thanks a lot, Aristotle, but we’re interested in documentation, not story-telling.”
Except your documents are the story of your company and your company's device.
Let me explain.
For every document within your Quality Management System, there is an expectation of some level of “traceability.”
What is traceability? Traceability is the process of leaving breadcrumbs—both upstream and downstream. For example, if your assembly process generates a record, you should be able to look at that record and determine its history. What Work Instruction was used? What Form was used to create that Work Instruction? What Procedure governed that Form?
It’s up to your organization to define the extent of traceability needed to meet all applicable regulatory requirements, but every document must be traceable at some level. And it’s that requirement for traceability that creates the overarching story of your company and your device.
Here’s how it happens:
Act 1: The Set Up
Section 4.2 of ISO 13485 - Quality Management System for Medical Devices is titled “Documentation Requirements.”
For medical devices, best practices for Document Management start in Section 4.2 of ISO 13485 - Quality Management System for Medical Devices. This section of the standard is titled “Documentation Requirements,” and it gives you a roadmap—a starting point. “The quality management system documentation shall include…” and then it gives you a list!
Now, let’s talk about one of the specific documents mentioned in ISO 13485 Section 4.2: the Quality Manual.
When you create your Quality Manual, you’re expected to lay out the scope of your Quality Management System, any documented procedures needed for the QMS, and a description of the interaction between those processes.
This is the Set Up.
The way a lot of companies do this is by listing out, or referencing, every Standard Operating Procedure (SOP) governed by the Quality Manual. Because you’ll want to show how you’ve met ISO 13485 requirements, there is often a table at the end of the document showing how each section relates to the requirements in ISO 13485.
Sweet, you now have a document that clearly lists your procedures internally, and shows how you meet requirements externally. In the next layer down—the Standard Operating Procedures—you’ll likely have references to each SOP’s specific Forms and Work Instructions.
When this is first set up, it’s a beautiful thing; it’s almost a 3D history of everything your company plans to do, from a quality standpoint.
You’ll learn to love traceability.
Act 2: The Conflict
Eventually, something will need to change, and that change precipitates the Conflict between old and new versions of a document.
When it comes to best practices, the first and greatest commandment is to have a single source of truth. You have to set up your document management system in such a way that released documents are easily distinguishable from obsolete or superseded documents
When you have documents stored in DropBox, SharePoint, Google Drive, your desktop, the file cabinet, the shop floor, and your email, at some point you will forget what the latest version or revision number is, unless you have a single source of truth, and you go to that source every time (please, don’t let it be your desktop.)
Pro tip: ditch the extra storage and use the single source of truth to pull the right version of the published document every time.
The second command is similar to the first—don’t duplicate information across documents.
Why not?
Think about it. If and when those changes come up, you don’t want to have to scour your entire QMS to find all the other places this changing information is written. Best practice: reference, don’t duplicate.
Act 3: The Resolution
Once you’ve made all the changes to your documents, it’s important to do two things:
-
Publish with due diligence - make sure the appropriate parties understand, approve of, and sign off on the change.
-
Supersede and/or Obsolete all instances of the previous revision/version of the new document.
And that takes us to the Resolution. Because if you’ve used a single source of truth, published with due diligence, and superseded all previous documents, there shouldn’t be any conflict left in your documentation. In fact, you should have a beautiful story to tell with great satisfaction during your next audit or inspection.
Tips for writing your story
Finally, let’s talk about the best way to write your story. In the medical device industry, we call this Good Documentation Practice, or GDP.
Everyone gets tripped up by GDP at some point. There are some do’s and don'ts that every medical device professional should know.
Good Documentation Practice Do’s:
-
Record the entries, whatever the activity is, in real time.
-
Always include a date next to your signature (and follow the date format in your procedure! Is “2/10/22” February 10th or October 2nd??)
Good Documentation Practice Don’ts:
-
Don’t use whiteout! Cross out mistakes with a single line so it is still legible.
-
Never backdate. If something is signed after the fact, use the current date and provide an explanation.
Greenlight Guru helps you tell your medical device’s story right the first time
When it comes time to tell the story of your device, you want to be sure it’s clear, concise, and above all, accurate.
With document management software from Greenlight Guru, you’ll never find yourself chasing down stakeholders or searching frantically for documents. Our QMS Software allows you to see your document structure in a centralized view and offers complete version history, e-signatures, and watermarks that automatically highlight a document’s status—so you know for sure everyone is working on the most recent version.
Ready to tell an amazing story about your medical device? Then get your free demo of Greenlight Guru today!
Looking for a design control solution to help you bring safer medical devices to market faster with less risk? Click here to take a quick tour of Greenlight Guru's Medical Device QMS software
Etienne Nichols is the Head of Industry Insights & Education at Greenlight Guru. As a Mechanical Engineer and Medical Device Guru, he specializes in simplifying complex ideas, teaching system integration, and connecting industry leaders. While hosting the Global Medical Device Podcast, Etienne has led over 200...
Related Posts
Leaning into Lean Documentation
What is a Document Control System for Medical Devices?
Introducing Document Comparison: Boost Audit Readiness, Accelerate Training, and Streamline Approvals
Get your free resource
Benefits of a Formal Document Management System
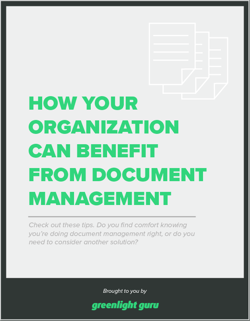