How to Create a Quality Manual per ISO 13485 (Plus Free Template)
A quality manual is one of the elements of a quality management system (QMS) required by ISO 13485:2016. While it isn’t a lengthy document, the quality manual plays a critical role in ensuring that users can navigate your QMS and quickly find specific documents and records.
In fact, your quality manual is essentially the table of contents for the rest of your QMS. Any stakeholders, both internal and external (like auditors or potential investors) should be able to use the quality manual to find where specific procedures or records are located within your QMS.
The quality manual should also provide an overview of your quality program—the company’s purpose and objectives for the QMS, roles and responsibilities for maintaining the system, documentation structure, and how your processes interact with each other.
That may sound like a lot, but the best quality manuals are actually simple and concise documents. Here’s what you need to know about creating one that meets the requirements of ISO 13485:2016 (along with a free quality manual template).
What is a quality manual and why do you need it?
Besides being a regulatory requirement, your quality manual is the document that helps you (and auditors or other stakeholders) navigate your QMS.
The requirement for a quality manual can be found in Clause 4.2.2 of ISO 13485:2016—and it’s a requirement for ISO 13485 certification. However, some people may point out that the term “quality manual” does not appear in the FDA’s Quality System Regulation. While that is true, it’s worth considering a closer look, even if you aren’t planning on obtaining ISO 13485 certification.
For one thing, the quality manual is extremely useful for both internal and external stakeholders, giving structure and form to an enormous amount of information. But the other reason you need a quality manual is that ISO 13485:2016 will soon be incorporated into the FDA’s new Quality Management System Regulation (QMSR) by reference, harmonizing the standard and the regulation.
And the QMSR directs MedTech companies to “document a quality management system that complies with the applicable requirements of ISO 13485.” In other words, if you plan to market your device in either the US or the EU, then you need a quality manual.
ISO 13485 quality manual requirements: 4 key elements
ISO 13485:2016 gives MedTech companies flexibility as to how they structure their quality manual, but regardless of the exact form, your quality manual will need to include these four elements:
-
The scope of the quality management system, including details of and justification for any exclusion or non application;
-
The documented procedures for the quality management system, or reference to them;
-
A description of the interaction between processes of the quality management system;
-
An outline of the structure of documentation used in the quality management system.
As we go through each of these, keep in mind that your quality manual isn’t meant to be a book-length document. Medical device manufacturers often feel they need to reference everything in ISO 13485 as they create their quality manual. And while that approach may technically satisfy the requirements for a quality manual, it may not create the most useful quality manual.
Employees, customers, regulatory agencies, investors, and other key stakeholders will be the main users of the quality manual. So it’s important that you create a streamlined document that someone can quickly and easily navigate, while still including the four main elements.
Here’s what to know about each of them.
1. The description of the scope of your QMS
The first required element of your quality manual is the scope of your QMS requirements. To begin, you might state: “This quality manual is for all ABC Diagnostics companies located at (list addresses).” You could then include a brief description or list of the activities performed at each of those addresses (design and development, internal audits, etc).
The scope of your quality manual should also include any clauses or sections that are excluded from your QMS, including a justification for each exclusion. Here’s an example of an exclusion statement: “As our products are not intended to be implanted, Section 7.5.5 does not apply.”
Be as clear as possible when documenting your rationales, as you may be required to defend them in an audit. Also, keep in mind that only aspects of clauses 6, 7, and 8 in ISO 13485:2016 may be excluded from your QMS requirements.
The scope of your QMS must also include, and define the roles and responsibilities of, any third parties you’re working with, such as manufacturing and sterilization firms, and provide their full contact details.
2. The list of QMS standard operating procedures
There are a number of standard operating procedures (SOPs) that ISO 13485 requires companies to document or reference in the quality manual, including, but not limited to:
-
Control of documents
-
Control of records
-
Internal audit
-
Control of non-conforming products
-
Corrective and preventive actions
-
Validation of computer software
-
Management review
-
Design and development
-
Validation of sterilization and sterile barrier systems (if applicable)
-
Identification and traceability
-
Feedback and complaint handling
It’s important to note that ISO 13845 does not require you to write out each of your procedures in the quality manual; the guidelines only specify a list or index of the company’s SOPs.
To meet the requirement, you can create an appendix within your quality manual called “Documented Procedures” and then list your procedures in a table format. This could include two columns, one to reference the section number or title within ISO 13485:2016 (7.4 Purchasing) and a second column to reference your procedure (SOP-06, Purchasing Procedure). It would look something like this:
ISO 13485:2016 Section |
Procedure Title/Number |
7.4 (Purchasing) |
SOP-06, Purchasing Procedure |
3. The description of process interactions
The objective of this requirement within your quality manual is to describe how your various processes interact with one another.
One of the simplest ways to depict this is by including process flowcharts that show the dependencies and interactions of your processes. For instance, your process for nonconforming material will be dependent on your process for incoming inspection, which depends on your purchasing process. That interaction could be represented like this:
The full flowchart will include all your processes, including design and development, management responsibility, post-market surveillance, and manufacturing, to name a few. But however you choose to represent the interactions between them, just make sure that it is clear how the different processes connect with and influence each other.
4. Document structure
Your quality manual will also need an outline of your document structure. It’s up to you how you want to structure your documentation, as long as you can clearly explain it in your quality manual.
However, a typical QMS structure can be visually represented as a pyramid. The quality manual sits at the top along with your quality policies and objectives. Below that are your documented procedures. Below that are the work instructions, forms, specifications, drawings, etc. that you need to carry out your procedures. And at the base of the pyramid are your quality records (such as records of internal audits). Together, it looks something like this:
Example of a QMS Hierarchy
Many people find this structure intuitive, as each descending level of documentation becomes more granular and the total amount of associated documentation increases.
Extra quality manual elements
Aside from the four required sections laid out in ISO 13485, there are some “nice-to-have” elements many companies include in their quality manual:
-
Your quality policy, which is a formal statement of the company’s commitment to quality and continuous improvement within their QMS.
-
A brief description of the company, its mission, and vision.
-
A list of any definitions or abbreviations used in the quality manual.
-
An organizational chart detailing job titles, though not necessarily who holds the title currently.
-
A list of the regulations and standards you are following. (This is especially important if your products are sold in multiple markets.)
And remember, if you’re looking for an example of a quality manual that you can use to build your own, check out our free quality manual template below.
Easily meet ISO 13485:2016 requirements with Greenlight Guru Quality
Creating a quality manual isn’t just a requirement; it’s an opportunity to deepen your understanding of your quality management system and how all your processes interact with each other. For smaller companies, it can be eye-opening to see everything that’s required by ISO 13485. And for a more mature company, that may be retroactively creating a quality manual, it may serve as notice that your QMS is not as well-organized and streamlined as you need it to be.
Whatever the case, you need QMS software that not only allows you to automate processes, link any element to another, and provide full traceability within the system, but also comes validated to the requirements of ISO 13485:2016. Remember, regardless of whether you want official certification to the standard, you’ll soon need to meet its requirements in both the EU and the US.
Now’s your opportunity to get ahead of harmonization. So get your free trial of Greenlight Guru and see what a MedTech-specific eQMS can do for your business.
Taylor Brown is a Medical Device Guru, certified Lead Auditor for ISO 13485, and a card-carrying Quality Nerd. She got her start in the industry as a technical writer and quickly became an audit readiness and support specialist, traveling around the United States to establish ISO 13485 compliant quality systems. She...
Related Posts
QMSR Explained: What FDA QSR & ISO 13485 Harmonization Means for Medical Device Companies
Ultimate Internal Audit Checklist: FDA QSR & ISO 13485 Audit Checklist
QMS Implementation: The Key Steps and Tips for Implementing an eQMS
Get your free Template
Quality Manual
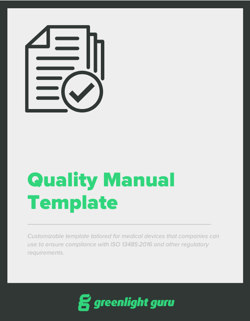