Why Training Compliance Matters for Pre-Market MedTech Companies
Medical device companies in the pre-market stage tend to put training compliance on the backburner. It’s not that there aren’t directions for achieving compliance—ISO 13485 devotes a subsection to training compliance, as does the FDA’s Quality System Regulations.
It’s just that there’s no straightforward answer to how you should go about fulfilling the obligations they list.
And when your company is focused on getting a product to market as quickly as possible, it’s easy to punt the ambiguous stuff and focus on building your device. I can’t say I’d recommend that approach, though.
So let’s talk about what training compliance really entails—and why you should start thinking about it sooner rather than later.
What are the training requirements at MedTech companies?
Section 6.2 of ISO 13485 lists the requirements for the training of employees:
-
Personnel performing work affecting product quality shall be competent on the basis of appropriate education, training, skills and experience.
-
The organization shall document the process(es) for establishing competence, providing needed training, and ensuring awareness of personnel.
-
The organization shall:
-
-
determine the necessary competence for personnel performing work affecting product quality;
-
-
-
provide training or take other actions to achieve or maintain the necessary competence;
-
-
-
evaluate the effectiveness of the actions taken;
-
-
-
ensure that its personnel are aware of the relevance and importance of their activities and how they contribute to the achievement of the quality objectives;
-
-
-
maintain appropriate records of education, training, skills, and experience (see 4.2.5).
-
As you can see, the requirements leave the execution of the training up to the company (if you’re wondering, the FDA’s requirements are even shorter and vaguer). This leaves companies a lot of leeway when it comes to training employees.
I’ve worked at multiple organizations where sometime in the first few weeks, a giant stack of papers landed on my desk—they were all the SOPs that could even remotely pertain to my job. Most of those were “read and understand,” but some of them I had to memorize and take a quiz on.
Does that fulfill the letter of the regulations? Probably. Does it fulfill their spirit? That’s up for debate. Frankly, the industry hasn’t really solved the problem of training; there isn’t a one-size-fits-all strategy for meeting both the letter and the spirit of the regulations.
The one thing I can tell you is that you really shouldn’t wait to begin establishing your training processes.
Why should you start training compliance early?
During the pre-market stage, MedTech companies often feel pressure to be agile, iterate, and move quickly to get things done.
Training compliance is the exact opposite of that ethos. It’s about “ensuring,” “evaluating,” and “maintaining.” Those are not exciting words. They imply a slow and careful pace that feels out of step with getting a product to market.
A lot of companies also know that training is not part of their pre-market submission, and that FDA won’t be looking at their training until further on down the road during an inspection. So, they decide to wait on it. Once the product is on the market, and they can relax for a moment, they’ll get around to training.
There are two points I want to make here.
First, this is a poor way to go about your business, just from a philosophical standpoint. Once you begin following the regulations from an external point of view—doing only what you think you’ll be checked on—you’re treading a dangerous path. That is a compliance mindset, not a quality mindset, and over time that will manifest itself in the quality of the product you bring to market.
Second, waiting on training compliance will actually slow you down at least as much as if you had worked on it from the beginning. It takes time to get any process right. You have to try it one way, see what problems crop up, and then iterate. Many times, usually.
So when you wait to create your training processes and start documenting your activities, you’re just beginning to make mistakes and learn from them—when you really should be perfecting an already-workable process.
To build the best medical device, invest in training your people
When you’re working on a medical device, it’s easy to forget that everything you do—design, development, pre-market submission, etc.—is someone’s responsibility.
And everyone on your team has certain competencies and comfort zones. That’s just human nature. So, deficiencies with the product could indicate that you’re missing a skill set or competency on your team.
For instance, let’s say you submit your 510k and FDA says you missed a specific validation that you need to do for this product. If you’ve been keeping up with your training compliance, when you get that feedback you can take a look to see whether your team is trained on the SOP’s related to that issue. If you haven’t been documenting and maintaining records of who is trained on what, that’s going to be significantly more difficult to figure out.
There’s a bigger picture component to all of this, as well. Training, like every other part of quality management, isn’t just about compliance. Taking training seriously from the start is part of establishing a quality mindset, and it keeps you focused on increasing the overall knowledge and skill level in your company. In our 2022 State of the Medical Device Industry benchmark survey, 23% of respondents said their biggest obstacle to quality management was underinvestment in education and training.
So it only makes sense to get the ball rolling with training early on. Send people to professional development, train them on new subjects, bring in people who are trained on specific items.
Focus on your people processes first, and your product processes are guaranteed to get better, too.
Simplify training compliance & streamline processes with Training Management Software from Greenlight Guru
The difficulty of establishing training processes and staying on top of documentation requirements is one of the big reasons training often gets less attention than it should.
At Greenlight Guru, we want to make focusing on quality—instead of compliance—as easy as possible. That’s why we built Training Management Software that tracks training and provides the evidence that the right people have been trained on a process, change, or other activity.
If you could use complete, accurate, and up-to-date access and visibility on all your training activities, then get your free demo of Greenlight Guru today.
Etienne Nichols is the Head of Industry Insights & Education at Greenlight Guru. As a Mechanical Engineer and Medical Device Guru, he specializes in simplifying complex ideas, teaching system integration, and connecting industry leaders. While hosting the Global Medical Device Podcast, Etienne has led over 200...
Read More Posts
Ultimate Guide to Training Management for Medical Device Companies
Understanding ISO 13485 Training and Competency Requirements
Streamline the right training, for the right people, at the right time. Introducing Greenlight Guru Training Management
Get your free PDF
Training Matrix Template
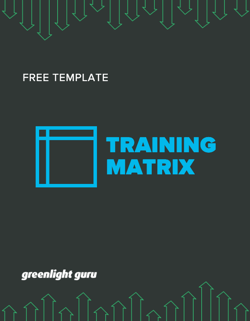