Do you consider your medical device company to have a culture of quality?
You may have heard me speak on this before. Quality is the heartbeat of everything we do as medical device professionals. When we put quality first, we’re ultimately putting our patients first and our businesses in a position for optimal success.
A culture of quality is arguably the best thing a medical device company can develop - here are three reasons why:
Adopting a quality culture improves medical device outcomes for patients
Let me tell you a story from way back in my early career about the first time I was able to make the connection between the work I was doing in product development and the real-world impacts, determined by its quality, that it has when used by a patient.
I had the opportunity to be present for the first clinical use of a product I had designed and developed. As far as clinical procedures go, it was relatively simple; however, when it came time for me to watch my device be used in real-time, on a real patient, I was terrified!
While the procedure itself likely took less than 30 seconds to complete, it felt like hours. It was the first time I really grasped the significance of the work I was doing and the critical importance that medical device quality plays in the life of a real human.
Since that moment, and in the 20+ years since, my mission or mantra has been centered on improving quality of life. This has come into sharp relief for many organizations across the world, maybe even especially more recently with the global health crisis we’ve all faced over the last year.
Technology has played a critical role in scaling and facilitating life-saving medical devices, allowing more people to be monitored or treated effectively. It has enabled us as manufacturers to deliver on that mission of improving the quality of life through world-class medical devices that provide better outcomes for patients.
Regardless of the circumstance, the first in-human trial is a major milestone for any medical device professional and their company, and should be treated with the same, if not more, level of gravity it deserves.
That means everyone involved in producing the medical device should support one another through a sustained culture of quality that enables your best work as medical device professionals. A quality culture demands a shared commitment of delivering quality outcomes.
In the context of developing a medical device, this means you’ve crossed all of your “T’s” and dotted every “I” prior to the product’s design transfer into manufacturing. This due diligence ensures that when the time does come for your device’s first in-human use, you have the highest level of confidence that your medical device will be safe and effective.
If you’re doing tests or other activities “just to fulfill a requirement,” you can easily lose focus of the real purpose of True Quality; this insidious mindset can unravel trust, team morale, and your culture in addition to putting your product in a highly undesirable position to succeed.
Why am I specifically mentioning this here? To save you from hastily rushing to your first in-human trial, skipping past key checkpoints that serve a critical purpose of ensuring your device is in fact ready to interface with patients. In my view, this is reckless, completely avoidable, and the opposite of what a True Quality culture is about.
Operating in a culture of quality enables innovation & technological advancements
How does operating in a culture of quality enable innovative devices and advancements? Well, start by considering what happens when there isn’t a culture of quality. Mistakes happen. Miscalculations are used. Important steps get missed out and ultimately, the safety and efficacy of your medical device suffers.
Pretty soon, a company is fighting fires. They’re busy investigating CAPAs, addressing audit findings, or reinventing the wheel when it was perfectly fine to begin with. In short, they don’t have time to focus on any further innovation of their medical device because they’re too busy reacting.
Adopting a culture of quality where the principles are clearly understood and reinforced by each member of the organization is paramount to operations running smoothly. Your team will have more time to focus on things like further learning, process improvements, and ideas that will drive innovation and technological advancements for your device.
I was fortunate to begin my medical device career at a world renowned company, Cook Medical, where there was a heightened focus on creating quality devices and delivering quality outcomes for patients.
Twenty years later, there is one core principle that we used to sustain our culture of quality: If you keep the patient at the center of what you’re doing, then True Quality becomes second nature.
The culture of quality that was established at that company was infectious in the best possible ways. We lived and breathed by the values that were important to us, both professionally and personally. That’s why I believe it’s so important to embed a personal attachment to the work you’re doing.
If you don’t fully understand your patients and how your medical device will impact their lives, take it upon yourself to do the research. Then take it a step further by considering it being used on your loved ones. Making it personal will force you to set new standards for what True Quality looks like and how you will achieve it.
Fostering a quality culture leads to better returns on investments & larger market share
There’s one thing all investors have in common: they want to make a return on their investment. Generally, they want to make that return in as short amount of time with the lowest amount of risk possible.
The journey of bringing a device to market is at least a few years, and that’s just to get to market. Return on investment? That can take much longer after the product reaches the market before those dollars start to hit any investor’s bank account.
Medical devices are a high-risk endeavor for investors. We’re talking about medical devices and emerging technologies with no proven historic metric of success. You then must account for the regulatory aspect of our job and potential issues of noncompliance, which can add additional business risk.
What if you could quell some of these commonly shared fears by investors? What if you could present clear evidence that proves you have followed all due diligence for a secure investment? What if you could give them visibility into your quality data to prove that your product is likely to succeed, thus is a strong investment?
Fostering a culture of quality can not only lead to a better return on investment, it can help you to attract worthy investors in the first place. Cutting corners or skimming over regulatory requirements will not be seen as an acceptable risk to savvy investors, whereas fostering a culture of culture in which your systems and processes prioritize quality will serve as compelling proof for most investors.
Support your culture of quality with a True Quality medical device QMS solution
When it comes to quality, communication and transparency are key ingredients of success. A culture based on True Quality means that knowledge is documented and easily accessible in a quality system that can be effectively managed by teams.
The only thing you may be missing is the right quality management solution, one that also prioritizes True Quality.
Greenlight Guru is the only medical device QMS software for the medical device industry, purpose-built to support your culture of quality by helping you produce, deliver, and manage a True Quality medical device.
Get your free demo of our QMS software today!
Looking for an all-in-one QMS solution to advance the success of your in-market devices and integrates your quality processes with product development efforts? Click here to take a quick tour of Greenlight Guru's Medical Device QMS software →
Jon Speer is a medical device expert with over 20 years of industry experience. Jon knows the best medical device companies in the world use quality as an accelerator. That's why he created Greenlight Guru to help companies move beyond compliance to True Quality.
Related Posts
Challenging “Conventional Wisdom” in Medtech R and D
CAPA: When to Take Corrective Action or Preventive Action?
Why the FDA Case for Quality Matters
Get your free infographic
Value of True Quality Infographic
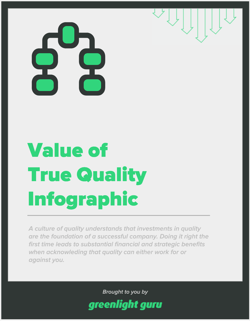