
It's easy to think of quality as a niche responsibility, requiring only the involvement of those working in quality-based roles.
But involving your entire medical device organization—and even suppliers and manufacturers—in the quality process can lead to better products, greater efficiency, and more engagement across departments.Total quality management (TQM) is a practice that many businesses use to involve their entire organization in the pursuit of utmost quality. But TQM doesn't just happen on its own.
There are several principles that uphold total quality management, each of which requires a commitment from each member of the organization. Let's start by looking at total quality management in a nutshell before diving into five key principles that TQM is built on and how to put each into practice.
What is total quality management?
Total quality management is the practice of promoting and ensuring excellence and safety in products by involving all relevant stakeholders, including but not limited to:
-
Employees
-
Leadership
-
Suppliers
-
Manufacturers
-
Customers
This practice involves all relevant stakeholders (manufacturing, marketing, product development, R&D, sales, purchasing, HR, etc.) working toward improvements to the business’s creation of goods and services. When successful, this unified approach makes it easier to monitor quality-related issues, no matter what department they originate in.
Let’s say someone on the production line notices a device part is faulty after it has already been sent to packaging. This person reports this issue to their manager, who then reports it to your quality team. The Quality Team finds a possible solution to the problem: the device will require either cooler storage conditions or a new adhesive. Without strong total quality management practices in place, your team may not have reported this problem in the first place and the faulty part may never have been fixed.
There’s more to total quality management than simply telling your team about the importance of quality. Implementation of TQM requires scalable quality management tools, like QMS software purpose-built to serve the unique needs of the medical device industry. Total quality management tools make prioritizing quality more feasible by streamlining various aspects of quality and quality-related processes.
5 key principles of TQM
But before you start investing in quality tools, you must know the fundamentals of implementing a total quality management culture at your organization. These five principles are the pillars on which total quality management stands and operates, each one supporting quality in a different way.
Principle #1: Managers spearhead total quality management
Total quality management doesn’t happen through sheer will or magic. An engaged team is a must for TQM to be performed successfully—and engagement starts at the top. Your leadership team must fully understand the processes involved in TQM, stay on top of training their teams, and, ultimately, act as ambassadors for total quality management.
There are a number of tools that managers can use to manage quality, but few are as effective as the Deming Cycle, also known as the PDCA (or PDSA) cycle. The Deming Cycle is a scientific approach to product management, emphasizing continuous improvement and learning.
The Deming Cycle involves four main steps that guide your management team through identifying, analyzing, and acting on quality issues:
-
PLAN: Examine your current product for flaws, and map out what improvement(s) you want to make. Think of these improvements as the goals of your project, as everything you do will serve to make these improvements a reality.
-
DO: Test out the improvements and necessary changes mapped out in the previous step. If you are able, make sure the changes are as minor as possible to ensure flaws are easier to detect. Also, don’t forget to include a control in each experiment in each experiment performed.
-
STUDY: What were the results of the tests, and did they align with your predictions? If the product didn’t improve, study every angle to determine the “why” behind this. It’s also important to note if the product improved in an unexpected way, because this information could help in future experiments or improvements.
-
ACT: Take what you’ve learned from testing, and implement any necessary changes with other products, services, or departments if possible.
The preceding steps play a pivotal role in a manager’s ability to quickly identify flaws, perform tests, analyze the findings, and act on the best course of action—in other words, create higher-quality products and processes.
Principle #2: Employees are supported by total quality management tools
Total quality management is “total” only if everyone is on board. This includes all employees, not just those in management roles. Don’t worry, there’s a pillar for that.
The right training goes a long way when it comes to rolling out total quality management. It should include guidance on applicable regulations and standards as well as any company policies around quality practices.
For example, if your company is using a new project management tool to track quality-related issues, implement proper training practices to ensure that the tool’s used properly. Next, build a process around using that tool, and build it into your employees’ routines.
The best way to simplify and manage training is by integrating training into your quality management system. Connecting training activities to other areas within your QMS allows your team to easily manage related tasks, check the status and history of those activities, and gain valuable knowledge about the latest policies or compliance requirements. Regulatory knowledge plays a large role in ensuring quality, making a formal training management tool a must.
Beyond integrating your training into your QMS, there are a few additional quick steps you can take to involve employees:
-
Implement a suggestion scheme, which gives employees a way to submit ideas and improvements, no matter their job title. Quality-related improvements can come from anywhere, which is why a suggestion scheme is important. A suggestion scheme gives everyone a chance to help.
-
Lay out clear measurements for success. Employee quality wins could range from little victories, like promptly completing quality forms, to larger achievements, like identifying a quality- or risk-related issue.
-
Hire subject matter experts to drive strategic quality initiatives. Quality professionals can educate your management on best practices, making it easier for them to guide and support your entire team.
Treat the task of training your staff on total quality management like any other training—stay vigilant and run refresher courses on an ongoing basis.
Principle #3: Risk analysis is frequently performed in a total quality management environment
Risk analysis is a cornerstone of both quality and good decision making. The risk analysis process involves calculating the pros, cons, and potential cost (financial or otherwise) of any decision. With proper risk analysis practices in play, you can more accurately determine if a decision is safe enough to make.
Going back to our earlier scenario with the faulty product part, risk analysis would allow you to compare the risks of either changing the adhesive or the storage conditions of the product. A different storage facility might prevent the adhesive from coming undone. But will the adhesive still hold when the device is in someone’s home or in a hospital? And if the adhesive is replaced, will there be other climate-related impacts or potential allergen risks with the new adhesive?
Effective risk analysis methods will give you the framework to plan for, mitigate, and manage any risks that arise throughout the product lifecycle. By pairing the Deming Cycle with thorough risk analysis practices, you can better manage change so you’re not working from a reactive state.
You can create your own risk management strategy or use an existing one. Whichever route you choose, ultimately you want to ensure you have a clear-cut process in place that guides your team toward educated decision-making that yields high quality products.
Principle #4: Data visualization is a mainstay of total quality management
Visualizations make data easier to interpret and quicker to present to any stakeholders involved with your medical device. When you’re running numerous tests, analyzing results, and weighing risks, proper data interpretation is huge. After all, what good are tests if you can’t fully discern any meaningful trends from them?
There are a number of quality data tools that are used for total quality management, but few are as reliable and renowned as the statistical tools listed below. These seven statistical tools are a set of visual aids that make it easier to identify quality-related issues and dive into risk analysis:
-
A cause-and-effect diagram (or fishbone diagram) provides a streamlined view of various scenarios and tests and the outcome of the action taken. This diagram is especially useful during the planning phase, because it provides a quick overview of potential inputs and outputs.
-
A check sheet is a basic chart that allows an observer or participant to keep track of how many times something takes place. The check sheet is particularly helpful in the early phases of testing out a theory or looking for a cause.
-
A control chart is a line graph that details how a manufacturing or business process shifts over time. This chart is great to use after changes are implemented, because it provides a look at the impact of those shifts.
-
A histogram shows how often particular events happen during a set event, like an experiment or process. It simplifies the process of analyzing how one change impacts the outcomes within a single process. This is especially helpful if you’re trying to determine how process changes impact outcomes.
-
A Pareto chart is a type of bar graph used for examining similar data points across various sample sets. For example, you could use a Pareto chart to compare the number of manufacturing defects that occur when using different adhesives.
-
A scatter diagram is a visual that depicts two variables on an X/Y axis to look for patterns or correlations. This visualization is particularly useful when you’re trying to look for any relation between two different events or sets of data.
-
Stratification is a method used to compare numerous data sets from different sources. This technique is useful for comparing data after experiments, but it’s also helpful when trying to find any risk-related trends while looking for a root cause.
The best QMS platforms for total quality management have visual tools already embedded within its software architecture to allow for fast, data-driven decision-making. For example, Greenlight Guru's change management and end-to-end traceability makes it possible to see all connected processes and artifacts within a single view so that teams can ensure they’re working in the most informed, up-to-date environment.
Principle #5: Total quality management prioritizes the patient
The patient is ultimately the deciding factor in whether or not your product succeeds. Total quality management enables continuous improvement and commitment to a high quality product, which is one part of the success equation.
Focusing on customer feedback allows you to make meaningful and necessary changes to your product that reflect the wants and needs of the end user. Be sure to make note of any product reviews or feedback you’re currently receiving, as this information can be used as a great jumping-off point when subscribing to the Deming Cycle. This prioritized focus on the patient, coupled with a focus on quality, completes the success equation for achieving total quality management success.
Consider working with a quality management vendor that has a customer success team with knowledge and experience in medical device total quality management best practices. The value and knowledge of this extension of your own team can be leveraged to help you better achieve optimal patient outcomes.
These subject matter experts can translate customer communication into actionable activities, provide best practices related to your current QMS processes, particularly those specific to managing customer feedback, suggest process improvements, and establish customer-centric business practices.
Both suppliers and your manufacturers play an integral role in your product life cycle, too. Make sure to involve them in discussions about total quality management practices that pertain to materials or manufacturing processes—and celebrate successes together!
Put total quality management best practices into action
Total quality management isn’t a one-and-done process. TQM is a never-ending, collective effort made by your entire medical device company and is united by one shared goal: to create true quality medical devices that save and improve patient lives.
The best QMS software will make following total quality management principles easier by offering valuable insight into the entire product life cycle, enabling you with powerful knowledge about your system, processes, and product to make informed, data-driven decisions that lead to high quality outcomes.
Greenlight Guru is the only QMS purpose-built for MedTech and perfect for any company looking to roll out a total quality management approach. The purpose-built QMS platform stays up to date with the latest regulations and standards, making it easier for you to achieve and maintain compliance while also offering dedicated workflows for every quality subsystem involved throughout the product life cycle so that you can achieve that shared goal of creating a quality product for patients.
Get your free personalized demo of Greenlight Guru QMS Software →
Looking for a QMS solution to help you bring safer medical devices to market faster with less risk? Click here to take a quick tour of Greenlight Guru's Medical Device QMS software
Taylor Brown is a Medical Device Guru, certified Lead Auditor for ISO 13485, and a card-carrying Quality Nerd. She got her start in the industry as a technical writer and quickly became an audit readiness and support specialist, traveling around the United States to establish ISO 13485 compliant quality systems. She...
Related Posts
Understanding the Quality Control Process in Medical Device Manufacturing
How to Use the MDSAP Companion Document
13 Tips For Audit Etiquette Every Medical Device Company Should Know
Get your free resource
Total Quality Management 4-in-1 Tool
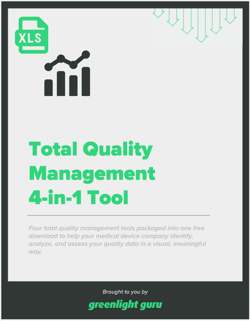