How to Improve Detecting, Correcting, and Preventing Nonconformances
If you work at a MedTech company, nonconformances are a fact of life. As long as there is still a human element in the development and manufacture of medical devices, there will be nonconformances.
But that doesn’t mean you should passively accept their inevitability. Product or processes that don’t meet specifications can have serious downstream effects, so detecting, correcting, and preventing nonconformances is extremely important for both patients and your business.
So, let’s take a look at how you can sharpen your nonconformance process and quickly identify and fix nonconformances before they become a larger issue.
BONUS RESOURCE: Click here to download a free Nonconformance Report Template.
What are the types of nonconformances and how do you identify them?
In MedTech, a nonconformance is a product or process that doesn’t fulfill a specific requirement established by a company, such as a disconnected process or defective product. For example:
-
A manufactured product that doesn’t conform to specifications and is identified during the quality control process is a nonconforming product.
-
A machine that is not placed on the proper setting and produces imperfect materials is a nonconforming process.
You may also experience nonconformances from parts or materials you receive from a supplier. If those materials don’t meet your specifications, they are also nonconforming products.
Given that they can occur in process or product, before or after manufacturing, there’s more than one way to detect nonconformances.
The different processes and activities that could turn up a nonconformance include your:
-
Supplier management procedures
-
Quality control inspections
-
Management reviews
-
Complaints process
Once a potential nonconformance is identified, it is important to initiate an investigation promptly to assess the root cause and impact on product quality, safety, and regulatory compliance.
How should you respond once you’ve detected a nonconformance?
As soon as you’ve identified a nonconformance, the first step you need to take is containment.
Containment (or control) of the nonconformance needs to happen immediately, and typically involves isolating the nonconforming product or stopping the nonconforming process(es) until the issue is resolved.
In parallel with containment, you should also begin a root cause analysis (RCA) to get to the bottom of what has caused the nonconformance. There are a number of RCA methods out there, such as the “5 Whys” or the fishbone diagram, but the goal of any RCA is the same: to figure out the primary cause of the problem and why it happened in the first place.
If you’re investigating a product nonconformance, you’ll also want to decide on the “disposition” for this nonconformity. Disposition is simply another way of saying what you’re going to do with this nonconforming product.
Typically, a nonconformity will fall into one of five disposition categories:
-
Scrap: Used when you decide to destroy a product instead of maintaining use of it.
-
Return to supplier: Used when the supplier ships the wrong component or piece and it must be returned. Some companies use the phrase “Return to Vendor” or “RTV” for short.
-
Downgrade: Used when a problem is found with a new version of a medical device following a change. Until a solution is identified, the previous version is to be used.
-
Use as is: Used when an unimportant defect is found with one of your products, such as a cosmetic flaw, and it’s determined that the product can still be used as intended.
-
Rework: Used when a product fails to meet certain stage requirements during quality assurance testing, but a correction can be made that still allows it to meet specifications after retesting. (Note that you must document said rework in your device history record (DHR)).
Even if you take minimal action, you must track all actions taken with regards to the nonconformance. If you find yourself scrapping more products than usual, for example, you may be on the trail of discovering a process nonconformance rather than a product nonconformance.
But remember, disposition is what you do with the nonconforming product. It doesn’t refer to how you go about fixing what’s causing the nonconformance. For that you’ll need to perform corrections and/or corrective action.
What is a “correction” and how is it different from a “corrective action”?
A lot of people in MedTech find the use of “correction” and “corrective action” confusing, and rightfully so. The two terms sound like they should be interchangeable, and they’re closely related.
But correction and corrective action don’t refer to the same activities, so let’s look at them individually.
What is a correction?
A correction refers to the immediate action that you take to fix a nonconformance. Corrections may include performing retraining activities, clarifying work instructions, or refining nonconforming products to meet quality standards, among other things.
However, corrections focus on rectifying the specific problem at hand; they don’t necessarily address the underlying cause of your nonconformance.
What is a corrective action?
A corrective action is taken to fix the underlying cause of the problem and prevent it from happening again. Corrective actions are usually more comprehensive and are intended to eliminate the root cause of the issue and prevent any future recurrence of the problem.
Corrective actions could include redesigning a process, adding a new inspection step, or switching suppliers.
Corrective actions are part of your CAPA (corrective and preventive action) process, and they’re not always necessary. For a single nonconformance, you probably won’t need to open a CAPA; you can handle it through your nonconformance process.
However, if the nonconformance indicates a systemic issue or resulted in an adverse event involving your product, then you may need to open a CAPA to get to the bottom of the problem and ensure it doesn’t happen again.
In sum:
-
A correction is the immediate fix for the nonconformance.
-
A nonconformance may lead to a CAPA, which will require a corrective action to fix the source of the problem and prevent it from recurring.
How do you prevent nonconformances in the first place?
As I said before, until robots are doing all the work, we won’t be able to eliminate nonconformances (and maybe not even then!).
That said, there are several ways you can prevent nonconformances from becoming a regular and painful occurrence.
Practice good supplier management
You rely on your suppliers to send you high-quality products that meet your specifications. Anything less puts your company and your device’s end users at risk.
The best way to ensure that your suppliers aren’t continuous sources of nonconformances is to properly evaluate and qualify them before you begin doing business. Monitoring suppliers and managing your relationship is important as well, but doing the work up front to ensure you’re working with a great partner will help eliminate preventable issues with nonconforming product or services.
Carefully consider inspection criteria
The choice of a supplier isn’t the only way to help prevent nonconformances with your parts and materials. Choosing the right inspection criteria will also help prevent issues.
You don’t want to be checking in parts, putting them on the shelf, and then discovering three steps later in the process that there’s a problem. There are standards out there that you can apply to improve this process, such as those found with acceptance quality limit sampling plans.
Pay attention to design transfer
You need to be thorough about describing your manufacturing criteria and requirements during design transfer. Nonconformances often occur where design transfer isn’t well-thought-out.
A good job of design transfer helps prevent future nonconformances by informing manufacturing resources of what’s important about the product. Actively working to improve that transfer of knowledge will eliminate preventable nonconformances and make everyone’s lives a lot easier.
That’s why at Greenlight Guru, the dedicated nonconformance module in our QMS connects directly to the manufacturing floor. This way, an event that occurs during production can be immediately logged on the floor and sent to Quality to determine next steps.
BONUS RESOURCE: Click here to download a free Nonconformance Report Template.
Greenlight Guru simplifies managing and correcting nonconformances when they do appear
It’s not always the nonconformance itself that’s a big deal. Sometimes the most difficult part of a nonconformance is efficiently documenting and managing the nonconformance process.
With Greenlight Guru’s eQMS, you’ll have a solution built specifically for the MedTech industry. That means you’ll have a defined workflow for handling nonconformances that will guide you through the essential steps while allowing you to establish the roles and permissions that control your specific process.
You can even assign investigation tasks to external users like contract manufacturers or other critical suppliers. You’ll be able to quickly and easily collaborate on nonconformances, CAPAs, and complaints, sharing information instantly and getting e-signatures for approvals.
To see how it works, get your free demo of Greenlight Guru today ➔
Etienne Nichols is the Head of Industry Insights & Education at Greenlight Guru. As a Mechanical Engineer and Medical Device Guru, he specializes in simplifying complex ideas, teaching system integration, and connecting industry leaders. While hosting the Global Medical Device Podcast, Etienne has led over 200...
Related Posts
3 Key Steps for Supplier Risk Assessment in MedTech
Nonconformance (NC) and CAPA: When Should You Use Each Process?
We Achieved ISO Certification! Now what?
Get your free resource
Nonconformance Report Template
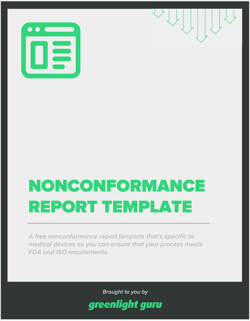