How to Integrate UDI into a Quality System for Your Medical Device
Unique Device Identification (UDI) is all about ensuring traceability quality in medical devices. However, integrating it into your quality system will require plenty of attention to detail.
Why? Because UDI touches just about every part of your medical device manufacturing procedures.
Though we cover everything related to UDIs in our Ultimate Guide to UDI for Medical Devices it’s never a bad idea to double click on some of the specifics.
In order to avoid falling out of compliance with UDI requirements, it’s essential that you’re reviewing the regulations, taking a holistic approach to the widespread impact of UDI, and establishing a quality plan for integrating it into your QMS.
Read the regulations for UDIs in quality systems
It’s never a good idea to start making plans without knowing what’s being asked of you. That’s especially true when it comes to UDI regulations, as that answer could change drastically depending on who’s asking.
In the US, FDA’s implementation of a UDI system is effectively complete, as the final deadline for Class I devices has come and gone. Thankfully, this means you’ll also find the greatest level of guidance and explicit legislative requirements of mostly any market’s UDI system.
The UDI Rule impacts the following areas of 21 CFR:
-
801 Labeling
-
803 Medical Device Reporting
-
806 Medical Devices: Reports of Corrections and Removals
-
814 Premarket Approval of Medical Devices
-
820 Quality System Regulation
-
821 Medical Device Tracking Requirements
-
822 Postmarket Surveillance
-
830 Unique Device Identification
In the EU, the full implementation of its Medical Device Regulation (EU MDR) is still very much in-process. Suffice to say that the regulatory requirements for UDI will impact nearly all areas of its various annexes and requirements.
For that purpose, the legislative bodies have released a new guidance document, MDCG 2021-19: Guidance note integration of the UDI within an organisation’s quality management system. Reviewing this guidance will help keep you on top of the upcoming and ongoing changes as it pertains to UDI implementation.
You can learn more about the UDI requirements for various global markets in our brand new Ultimate Guide to UDI for Medical Devices.
Understand how UDI connects to a quality system
Though it may seem like a subset of labeling activities, UDIs touch just about every element, department, and process contained in a quality system. In order to effectively plan for integrating UDI into your quality system, your team will first need to identify each of the functional areas expected to feel the change.
Though each company is unique, there are several major sections of every QMS that will require your attention. Remember that each of these changes will need to be validated, a process which may differ in complexity depending on your device.
Design and Development
It’s clear that UDIs are in no way intended to be an afterthought, so it’s best to incorporate them as early as possible, specifically as another design control for your development team. Not only will this be helpful as design inputs, it also will provide ample lead time to all affected departments and personnel.
Production
Another key area for focus will be the manufacturer’s decision of when, where, and how a UDI carrier will be applied to a product. Whether it’s directly on the device, or included in the labeling, both routes will have differing levels of packaging requirements. Regardless, make sure to include those specs in your device master record.
Postmarket Surveillance
A primary driver for UDI systems worldwide has been a faster and more efficient response to adverse events and product recalls. It makes sense that serious incident reports, field safety, corrective actions, and customer complaints, must be tracked and linked to all UDI activities.
Supplier management
In addition to the usual supplier management responsibilities, companies must now also account for new economic operators, such as your GTIN provider, issuing agency, distributors, authorized representatives, or anyone else provided with UDI information. Remember that just because you’ve become a UDI expert, doesn’t mean they have.
Documentation and Records
UDI runs on data and documentation, so it’s a good thing your QMS does, too! As FDA’s Quality System Regulation (QSR), states, “The quality system regulation is premised on the theory that adequate written procedures, which are implemented appropriately, will likely ensure the safety and effectiveness of the device.” Allocate loads of time for updating SOPs and linking UDIs for required traceability.
Develop your quality plan for UDI integration
Creating a plan for UDI integration into your quality system is essential, as it helps to ensure total compliance across the board. It also will be unique to each organization’s strengths and weaknesses for UDI, whether that’s related to the day-to-day processes or managing how larger systems feed into one another.
For some, UDI implementation may require substantial effort to revamp the QMS, as well as subsequent training and education for existing personnel. For others, your internal processes may already be set up for the levels of documentation or auditing required to implement UDIs.
With that in mind, we’ve created an example of a quality plan for integrating UDI into a QMS. Keep in mind that the steps and the order in which they’re followed may be different for your medical device company, and that this is only a suggested plan.
-
Read and assess regulatory requirements for UDI and QMS.
-
Establish internal roles and responsibilities for all activities related to UDI implementation. For each new role, define the necessary education, background, training, and experience required to perform the duties. Additionally, identify training needs, train the people in these roles, and document all training records.
-
Establish which type of UDI carrier will be utilized, such as ID/linear barcode, 2D barcode, RFID, etc.
-
Determine who the designated issuing agency will be, as well as any other economic operators or third party vendors involved in the UDI activities.
-
Validate the above list of economic operators the same as you would any supply management.
-
Define processes for UDI labeling, including design controls, direct marking, packaging, documentation, and traceability.
-
Define quality processes for UDI database management, such as for GUDID or EUDAMED.
-
Perform gap analysis on current QMS to uncover potential bottlenecks for UDI activities.
-
Generate new SOPs for quality systems, and be sure to validate all processes the same as dictated by your change management practices.
-
Perform regular quality audits on all parts of the system to ensure UDI integration is functioning properly.
Plan for the future of UDI integration and MedTech Lifecycle Management with Greenlight Guru
UDI implementation is no easy feat — it requires a whole new level of traceability and document management capabilities from your QMS.
Now, with Greenlight Guru, your team can achieve closed-loop traceability throughout your entire quality system, allowing you to easily make connections and understand key relationships within your QMS.
Thanks to Greenlight Guru’s MedTech Lifecycle platform, the integration of cross-functional teams, processes, and data throughout the product lifecycle means you’ll be able to effectively audit those UDI additions to your SOPs, as well as proactively overcome execution gaps and accelerate success.
If you’re ready to get serious about UDI implementation, contact us today for your free personalized demo →
Etienne Nichols is the Head of Industry Insights & Education at Greenlight Guru. As a Mechanical Engineer and Medical Device Guru, he specializes in simplifying complex ideas, teaching system integration, and connecting industry leaders. While hosting the Global Medical Device Podcast, Etienne has led over 200...
Related Posts
GUDID 101: Everything You Need to Know About FDA’s Global Unique Device Identification Database
Ultimate Guide to UDI for Medical Devices
Basic UDI-DI: What is it and How to Assign it for Your Medical Device
Get your free eBook PDF
Ultimate Guide To UDI for Medical Devices
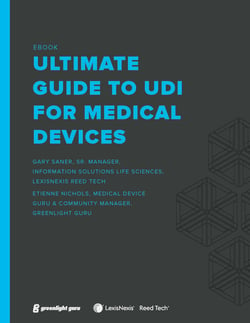