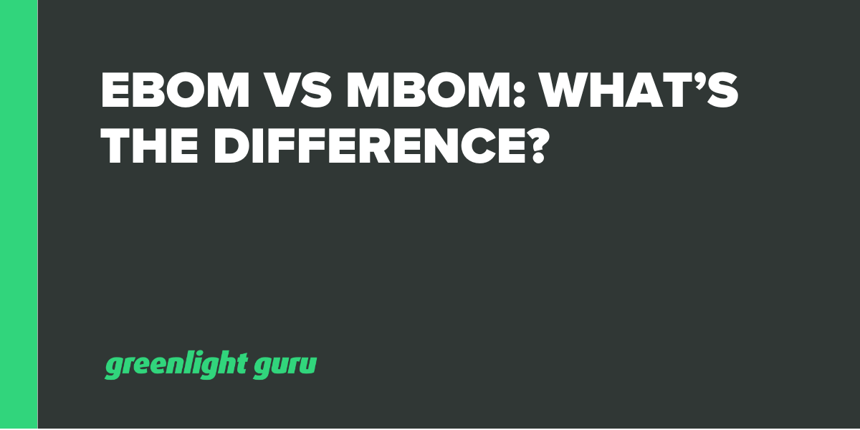
A bill of materials (BOM) contains all the materials and parts required to build your device, as well as directions for how to use them and where to acquire them.
However, a BOM will go through different iterations depending on what stage of the product lifecycle your device is in. That’s why some MedTech companies use terms like engineering bill of materials (eBOM) and manufacturing bill of materials (mBOM).
In this article, we’re going to cover the differences between these two types of BOM. But it’s important to remember that as we get into the distinction of eBOM vs mBOM, these terms aren’t describing entirely different things.
So, let’s dive into the distinction between the two and what you should know about creating and managing your BOMs.
What is an eBOM?
The eBOM is typically created by the product engineering team during the design and development process. Your eBOM will include all the parts and subassemblies of the final product. In other words, every component that the product needs to work correctly should be in the eBOM.
Because your eBOM is being assembled during design and development, it’s often generated in tandem with CAD or EDA tools and is organized around the design of the product. It may include engineering information about product specifications, tolerances, quantities, units of measure, and related engineering standards.
However, it usually doesn’t include packaging, instructions, or manufacturing consumables, as those may not yet be known.
What is an mBOM?
The mBOM is created for manufacturing purposes, and its structure reflects the way the product will be manufactured.
The mBOM will typically be organized into subassemblies reflecting the manufacturing process. For example, if you were to use a dozen of the same screws in your product, the eBOM might list them all as the same line item with a quantity of 12.
But that would tell you nothing about how those parts relate to each other. An mBOM, on the other hand, would likely list each screw in the subassembly where it’s used in the manufacturing process.
The mBOM also includes components that are necessary for manufacturing and purchase planning. That may include things like manufacturing consumables, tools, and fixtures that are not shipped with the product. It may also include things like packaging materials and instructions that are shipped with the product but might not be documented in the eBOM.
eBOM vs mBOM: how do they relate to each other?
Remember, the eBOM and the mBOM don’t exist in opposition to each other.
In the most basic sense, your eBOM will become—or at least heavily inform—your mBOM. Everything that’s in your eBOM will need to be in your mBOM, but the mBOM will likely include more information about how to manufacture this device and it may be structured differently.
Here’s an example of how this might look in practice:
Let’s say you use a BOM-building software solution, like Greenlight Guru’s Products workspace, during design and development. As you go through this early phase of the product lifecycle, you begin building your BOM in that workspace, which is part of your quality management system (QMS). This BOM would technically be known as your eBOM.
However, once the device is ready to be manufactured, you might need to export your BOM to a manufacturer’s ERP system. That “new” BOM will include everything in your eBOM. But in order to use it for manufacturing, you’ll add things like the manufacturing consumables or tools or packaging that may not have been included while you were in design and development. You might also change the structure to group items and materials differently.
So, the eBOM you’ve already created, plus whatever else you need to manufacture your device, equals your mBOM.
The question of eBOM vs mBOM comes up so often because there are no hard and fast rules for handling them and everyone treats them a little differently. Just remember, a BOM is a BOM is a BOM. You don’t have to get too caught up in naming conventions to build a bill of materials that will help you make good decisions about purchasing, inventory, and manufacturing for your product.
In fact, the way you create and manage your BOM is much more important than what you’re calling it at any given time.
How should a BOM be managed at a MedTech company?
A lot of early-stage MedTech companies will be drawn toward a tool like Excel for managing their BOMs. It’s cheap, and a spreadsheet seems perfect for listing a bunch of items and materials and their quantities.
The problem—whether you’re managing an eBOM or an mBOM—is that spreadsheets create information silos. That leads to multiple issues. One being that spreadsheets are not automatically updated, and you can’t always be sure you’re working with the latest product information. The other is traceability.
When you’re building a bill of materials in disconnected systems like spreadsheets or other general purpose tools, you can’t easily link documents, specifications, and drawings to items in each of your BOMs. Pretty soon you’re left with a tangled web of items and attachments instead of a clean and clear BOM.
What you really need is a system that allows you to build your BOM while staying connected to your QMS and design controls. You need a system that lets you easily share your BOM, item, and finished good information with an ERP. You need a tool that lets you export your BOM so you can easily incorporate it as part of your device master record (DMR).
And regardless of whether you’re talking about an eBOM or an mBOM, it needs to be accurate. The more accurate and complete a BOM is, the easier it is to make good decisions about purchasing, inventory, and the manufacturing of the product. A well documented BOM streamlines the way you collaborate with supplier vendors and make changes to the manufacturing of your device.
Create and manage your BOM in Greenlight Guru’s connected eQMS platform
Fortunately, you now have a place to build, manage, and share your BOMs—one that’s fully connected to your QMS and easily allows you to incorporate your BOM into your DMR.
With Greenlight Guru Products, not only can you build multi-level BOMs, you can easily link them to your documentation and design controls, all within the same intuitive platform. And when you need to export that BOM, you can download it as a CSV or PDF.
If you’re ready to see how much easier it is to build and manage your BOM on a single, fully connected platform, then get your free demo of Greenlight Guru today.
Niki Price is a Medical Device Guru who has spent her entire career working with different types of medical devices. She began her journey in production, which is where she discovered how important and fulfilling this line of work was to her! Spending time in both Quality and R&D, she enjoys the product development...
Related Posts
Making the BOM & Design Controls Connection
What is the Best Way to Structure a Risk Management File?
How to Create a Clinical Evaluation Report (CER) under MEDDEV & MDR (Part 4 of 4)
Get your free resource
Device Master Record (DMR) Checklist