Quality Management Plan - How to Create Yours (Tips & Best Practices)
Technically speaking, you can launch a product without a quality management plan—but most of your go-to-market efforts will feel as though you’re shooting from the hip and hoping you don't miss.
Without an established quality management plan in place, you'll be faced with a number of potential unknowns and risks, any of which could derail your project. Manufacturing issue that results in nonconforming product? Slow complaint handling process that takes your product off the market? Poor training practices that lower personnel competence? All of these unfortunate scenarios can be prevented by a solid quality management plan.
Prioritizing quality matters when you're in a competitive market where every second counts and your reputation is critical. With a quality management plan in place, you're setting yourself up for an organized, predictable start. The best quality management plans provide a reliable framework that could mean the difference between hitting product deadlines and failing to launch at all.
This article provides a blueprint you can use to create a quality management plan that enables your company to achieve quality goals, redirects you if you go off course, and places your medical device in a position to excel in the marketplace.
Structure your quality management plan according to internal quality audit findings
Performing an internal quality audit allows you to check for any potential quality issues or unforeseeable roadblocks you may encounter after your quality management plan is put in motion.
From there, you can create a quality management plan that accounts for potential areas of concern that were uncovered during the audit.
Follow these tips to conduct a quick yet reliable quality management audit:
-
Avoid the immediate temptation of hiring a third-party auditor if possible, and instead, rely on your own internal team to structure the quality audit. This internal team member could be a quality manager or team lead who understands how the company functions and has a good understanding of the applicable regulations and standards.
-
Make a list of every team that will be impacted by the quality audit and give as early of notification as possible. Audits tend to go smoothly when everyone is on board and prepared. Your role is not FDA Inspector, so a surprise inspection is not necessary and ultimately will provide little value as compared to the high value that can be gained from a well-executed quality audit.
-
Implement an electronic system for documenting your findings. Don’t rely on a pen and paper. The last thing you want is to lose everything or forget where key documents are stored. A lazy quality audit will turn into a sloppy quality management plan.
-
Avoid the costly mistake of conducting an internal audit at the end of the year. Quality audits deserve your full attention, so make sure you give this activity proper due diligence. A good rule of thumb is to perform quarterly internal audits, if possible, to stay on top of any potential issues or shifts before they become systemic.
An internal audit is more than a to-do list item. If it feels like a chore, try to view your quality audit as an opportunity to improve your product, processes or even company culture. This simple mindset shift can help you and everyone involved get the utmost value out of the exercise and ensure you are prepared for the potential unannounced audits to come.
Determine the project scope that your quality management plan will follow
Building a quality management plan before understanding the scope of the project itself is putting the cart before the horse. You need to understand how big the overall project is before creating a plan to tackle it.
There are a few practices you can put into place to determine the scope and keep your quality management plan from under- or overshooting your project goals.
Before meeting with any stakeholders though, brainstorm an aggressive deadline for the project amongst your immediate team. Then, set a more conservative deadline and present it to the stakeholders. A conservative deadline helps you establish wiggle room and avoid any kind of crunch or late deliveries on promises.
When you do eventually meet with stakeholders to formalize your project scope, speak with each member to gain a clear understanding of their expected involvement in the project. Since your quality management plan will set the foundation for your project, you’ll want to make sure everyone’s on the same page before actually drafting the plan. Specifically, you’ll want to determine the following things during this meeting:
- What they’re hoping your project accomplishes
- If there are new markets they wish to enter with a product you’re working on
- How involved they plan on being with the project
And make sure to temper expectations as well. You know what your team is capable of. If certain stakeholders are asking for a reinvention of the wheel, remind them that’s not doable—or in your “wheelhouse,” per se.
Take note of any areas where your product and processes vary from what the market will need. If there are numerous discrepancies between your current product or processes and what customers want, the scope of your quality management plan will likely be extensive and unwieldy.
Draft your quality management plan
With the biggest preliminary tasks out of the way, it’s time to create your quality management plan.
There’s no one-size-fits-all template that exists, but typically, your quality management plan should include:
- Business case for your project. It’s important that you provide a breakdown of how this plan can be executed upon, with quality as the center stone. Will you assemble a board of advisors? Which quality management tools will you utilize during the project? What are the ongoing training activities that will be necessary for those involved in the project?
- Regulatory strategy. Your team needs to be aware of any regulations or standards that apply to your company and medical device in order to comply with the necessary requirements. Both regulations and standards dictate quality in a big way, so it’s essential your team has a good pulse on the regulatory landscape in which you’re playing.
- Agreed-upon communication process. Detail who will be the primary person of contact for your team if certain issues arise, as well as the preferred communication method. Your team should be able to reference the quality management plan and know how to communicate effectively about the details and progress of the project with the relevant members of the team.
- Alignment of team expectations. Align your team so that each member has a clear understanding of what’s expected of both their own role and other roles on the team, and how each part is contributing toward the overarching project goals. Keep in mind external stakeholders may also have expectations that also need to be considered.
- Quality management process. Detail how quality processes will be managed, including the procedures that should be followed for quality events. Reiterate who handles what issues and walk through example scenarios in which people encounter various quality issues and solve them.
Your quality management plan shouldn’t be a static document. If you notice something isn’t working out as planned, find a solution and update your plan to reflect those changes.
It’s important to note that any changes to your plan should be clearly documented then communicated to all stakeholders. Additional steps, such as training, may be necessary depending on the complexity of the change.
Identify resources needed to execute your quality management plan
Every quality management plan will require certain resources that must be in place before formalizing it, let alone executing it.
In order to make preparing and implementing your quality management plan easier and smoother, do the following:
- Adopt the best tools for the job. Do you have any project management tools or a quality system in place? If so, look at their capabilities through the lens of your quality management plan. Will these tools support your team's efforts in successfully executing the plan, or do you need a more robust solution? You’ll want the right quality management tools that are capable of enabling your continued growth and scaling with your company.
- Develop a material review board, if you don’t have one. A material review board (MRB) can serve as a valuable asset to your company by reviewing any quality issues flagged by employees and facilitating the change management process that may need to be taken. Quality issues are inevitable, and this MRB can help in both the short and long haul all while ensuring your quality management plan is adhered to.
- Confirm resource capacity. Assess the workload that your upcoming project will demand. Are there any new tasks, potential inefficiencies, or other reasons your current resources may not be able to handle? Perform trial runs of any new processes to get an even better idea of whether or not you’ll need additional hires.
It’s hard to predict with full accuracy if you have the necessary resources to carry out your quality management plan before putting it into practice. There’s a high likelihood you’ll need to make changes along the way after the plan is already in motion, which should not derail your plan so long as you prepare accordingly and communicate effectively when there is a pivot.
Put your quality management plan into action
The preliminary work of creating your quality management plan is done; now it’s time to actually put your plan into action. The right quality system makes it easy to create, implement, and follow your quality management plan.
The best QMS software will enhance your efforts by allowing you to operate within controlled environments through medical device-specific workflows designed to support your project, enabling you to securely store and easily access documents, communicate within and across teams, and produce a safe and effective medical device.
Greenlight Guru offers purpose-built MedTech Solution. Greenlight Guru's Quality Management Software automatically stays up to date with the latest regulations and standards, removing the burden of achieving and maintaining compliance so you can focus on developing the highest quality of products possible.
Implementing a quality management plan is a significant undertaking that justifies an investment in quality to more easily and efficiently manage your project tasks. See how Greenlight Guru can make the process of rolling out your quality management plan seamless, enable optimal team communication, and reduce your chances of costly mistakes with a free personalized demo of our QMS software →
Looking for an all-in-one QMS solution to advance the success of your in-market devices and integrates your quality processes with product development efforts? Click here to take a quick tour of Greenlight Guru's QMS software
Sara Adams has spent over 15 years helping MedTech companies prepare for FDA inspections and build strong quality systems. Her expertise spans startups and established organizations, where she has led teams through high-stakes audits, simplified compliance, and improved operations. Sara is skilled in Quality System...
Related Posts
5 Biggest Quality Mistakes (And How You Can Avoid Making Them)
5 Tips to Improve your Medical Equipment Quality Assurance Activities
Is It Possible to "Buy" a QMS?
Get your free resource
Medical Device Project Plan
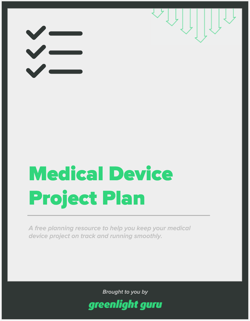