22 MedTech Experts Share Best Tips for Product Developers, QA/RA Professionals & Leadership Roles
The Greenlight Guru True Quality Virtual Summit is the must-attend experience for medical device quality, regulatory, and product development professionals who drive innovation in the most well-respected, high-performing companies in the market today.
The three-day, three-track event is taught by industry leaders who've taken medical device concepts through development, regulatory submission, and to market globally, within Fortune 500 companies and high growth startups.
We've rounded up responses by twenty-two MedTech experts from our lineup of speakers who want to share their keen insight, tactics, recommendations, and personalized tips for all medical device product development, quality, and regulatory leaders.
What You Need to Know to Get New Devices to Market with Less Risk
You can do better than just meeting compliance requirements. Get detailed advice from engineering and product development experts on how to build a quality foundation that allows you to innovate faster, provide full traceability throughout the device lifecycle, and create True Quality medical devices with less risk.
Get your free ticket to attend this track's sessions at The Greenlight Guru True Quality Virtual Summit.
What is the best piece of advice you could give a medical device company just starting out to help them ensure success throughout the entire product lifecycle?
Expert Tip #1
Develop Production post-production / Measurement, analysis, improvement processes as required in ISO 14971:2019 Clause 10 and ISO 13485:2016 Clause 8 to ACTIVELY gather and analyze data to improve the device and keep it up to state of the art throughout its lifecycle.
Ed Bills, ASQ Fellow, RAC, Medical Device Consultant
Attend this speaker's session: An Inside Look at Changes to the New ISO 14971:2019 from a Member of the Standard’s Working Group
Expert Tip #2
"Design for success." In addition to focusing on implementation of your medical technology (getting it to work), also consider issues such as connectivity, regulatory, and usability. Devices designed for collection and analysis of data (connectivity), developed with certified design controls (regulatory), and created from the end user's viewpoint (usability), enhance probability of commercial success.
Keith Drake Ph.D., VP of Business Development, Galen Data
Attend this speaker's session: Design Considerations to Maximize Medical Device Cloud Connectivity
Expert Tip #3
Before opening up your CAD software, work hard to define and refine your user and business needs, including the needs of regulators. Early interaction with regulators to align on grey areas of regulation and compliance can reduce over-design or under-shooting regulator expectations. Similarly, having a firm understanding of users’ “must haves” and “nice-to-haves” along with development risks, costs, and timelines provides a solid basis to enter design controls.
Chad Gibson, Managing Partner, CMD MedTech
Attend this speaker's session: When to “Flip the Switch”- Balancing Late Feasibility and Early Design Controls
Expert Tip #4
Talk to 100 potential customers. Let them help you figure out the right value prop for your product.
Scott Phillips, CEO, StarFish Medical, ViVitro Labs Inc.
Attend this speaker's session: Game Changing Product Definition Tactics
Expert Tip #5
Consider your regulatory, clinical, and market access plans/requirements all together as early as you possibly can.
Isabella Schmitt, Regulatory Affairs Consultant, Proxima Clinical Research
Attend this speaker's session: Best Practices for Preparing and Conducting Pre-Submission Meetings
Expert Tip #6
Make quality a priority from the start; start by providing your engineers with tools designed for the medical device industry. In November we released our State of Medical Device Product Development & Quality Management Report 2020, which found that 80% of organizations are asking their quality and engineering teams to “make do” with legacy tools. This old standard of treating quality as a checkbox activity must be forgotten. A cultural mindset shift must be made in order to keep quality at the core of a product’s life cycle from the start.
Jon Speer, Founder & VP of QA/RA, Greenlight Guru
Attend this speaker's session: 4 Quality Systems Must for Medtech Startups to Get Safer Products to Market Faster
Expert Tip #7
Define your product early. Too often a haze of indefinite product features cloud the implementation until too late in the process. The price of feature-flexibility is a confused and slow development process.
Milton Yarberry, Director of Medical Programs, ICS
Attend this speaker's session: How User Experience Design and Human Factors Engineering can Accelerate Product Development
What is the most common mistake you see companies make during the design and development process and what steps should be taken early-on to avoid it?
Expert Tip #1
Risk Management is an important and active aspect of product development and is not a CHECKBOX activity as performed by some. Done properly it can provide design information early in the process to reduce expensive design changes late in process due to risk. ISO 13485:2016 identifies the output of risk management is a design input. Therefore it must be completed early.
Ed Bills, ASQ Fellow, RAC, Medical Device Consultant
Attend this speaker's session: An Inside Look at Changes to the New ISO 14971:2019 from a Member of the Standard’s Working Group
Expert Tip #2
Recognizing device connectivity is no longer a "nice to have," but rather a "need to have" for commercial success. Cloud connectivity platforms receiving patient information (vital signs, treatment status) and device data (e.g., battery level) -- and communicating back to the device -- all in a regulatory compliant manner is a growing requirement for clinicians and patients.
Keith Drake Ph.D., VP of Business Development, Galen Data
Attend this speaker's session: Design Considerations to Maximize Medical Device Cloud Connectivity
Expert Tip #3
A common mistake occurring early on in the development process is entering formal design controls without having a firm grasp on the implications of doing so. Controlling the design too early can result in additional burden and overhead when unforeseen or deferred technical challenges arise. In addition to technical risk reduction, early diligence in program management and systems engineering will result in a less costly and more predictable design process.
Chad Gibson, Managing Partner, CMD MedTech
Attend this speaker's session: When to “Flip the Switch”- Balancing Late Feasibility and Early Design Controls
Expert Tip #4
Miss a key constraint. Lack the discipline to kill a product idea that doesn't check enough boxes.
Scott Phillips, CEO, StarFish Medical, ViVitro Labs Inc.
Attend this speaker's session: Game Changing Product Definition Tactics
Expert Tip #5
Perpetually designing a device in an engineering silo...before moving into any verification/validation testing...and before getting customer requirements. Best way to avoid this is to follow design controls as soon as you've decided this product is something marketable. This means you'll be establishing your MVP (minimum viable product) and designing towards that.
Isabella Schmitt, Regulatory Affairs Consultant, Proxima Clinical Research
Attend this speaker's session: Best Practices for Preparing and Conducting Pre-Submission Meetings
Expert Tip #6
With the regulatory landscape constantly changing, one of the most recent being ISO 14971:2019, focus can often be pulled away from Risk Management which is a huge mistake. I remember my first day on the job as a medical device product development engineer. During the orientation, I was shown a company video with a salient theme: the devices I was helping to develop could someday be used on a friend, family member or possibly myself. Imagine this from the perspective of a patient going in for any medical procedure. The patient probably thinks very little about the risks of the medical device they will soon come into contact with and often unknowingly, accepts the risks based on their health care provider’s advice. And this is exactly why effective Risk Management is so critical in the medical device industry.
Jon Speer, Founder & VP of QA/RA, Greenlight Guru
Attend this speaker's session: 4 Quality Systems Must for Medtech Startups to Get Safer Products to Market Faster
Expert Tip #7
Not understanding which shortcuts to take. You can scale your QMS, but you can't bolt-on risk management.
Milton Yarberry, Director of Medical Programs, ICS
Attend this speaker's session: How User Experience Design and Human Factors Engineering can Accelerate Product Development
What other tips, advice or best practices do you want to share with medical device product development leaders?
Expert Tip #1
The use of cross-functional teams with a wide range of knowledge and experience is key to product development. Clinical input, manufacturing input, purchasing input are all aspects of the good development processes. It is especially important that in the usability / human factors area that they examine the entire range of potential users of the device.
Ed Bills, ASQ Fellow, RAC, Medical Device Consultant
Attend this speaker's session: An Inside Look at Changes to the New ISO 14971:2019 from a Member of the Standard’s Working Group
Expert Tip #2
Acknowledge that cloud connectivity becomes part of your device from a market acceptance and regulatory viewpoint, and teaming with a cloud connectivity partner that supports your regulatory and compliance needs (pre-market clearance submission, audit activities) should be considered early in the product life cycle.
Keith Drake Ph.D., VP of Business Development, Galen Data
Attend this speaker's session: Design Considerations to Maximize Medical Device Cloud Connectivity
Expert Tip #3
Horses for courses. Never let a starter finish a project. Never let a finisher start a project.
Scott Phillips, CEO, StarFish Medical, ViVitro Labs Inc.
Attend this speaker's session: Game Changing Product Definition Tactics
Expert Tip #4
Ask questions! Don't try to be an expert in everything. And get advice from many sources...especially regulatory bodies!
Isabella Schmitt, Regulatory Affairs Consultant, Proxima Clinical Research
Attend this speaker's session: Best Practices for Preparing and Conducting Pre-Submission Meetings
Expert Tip #5
The industry is full of small medical device companies and startups that often require funding to cover the development costs associated with producing a medical device. With so many small players in the industry, the cost of a regulatory fine, product recall or device removal from the market is too much for a company to survive. This is why you must ensure that quality and compliance are at the heart of every process.
Jon Speer, Founder & VP of QA/RA, Greenlight Guru
Attend this speaker's session: 4 Quality Systems Must for Medtech Startups to Get Safer Products to Market Faster
Expert Tip #7
As a medical device startup, decide which skills to own and which to rent. There are many micro-domains in medical devices, and specializing in too many isn't specializing in any.
Milton Yarberry, Director of Medical Programs, ICS
Attend this speaker's session: How User Experience Design and Human Factors Engineering can Accelerate Product Development
How to Advance the Success of Your Devices Already on the Market
The best companies put True Quality first. Learn from leading quality and regulatory experts on how to stay ahead of an evolving industry, easily managing processes by providing the right visibility, and grow your devices and your business.
Get your free ticket to attend this track's sessions at The Greenlight Guru True Quality Virtual Summit.
What advice or tips would you give to medical device companies either preparing for an external audit or inspection for making sure it runs smoothly?
Expert Tip #1
Don't wait for FDA to show up at your door. If you are doing what you should be doing, whether it's "required" by FDA or not, you have nothing to worry about and you should say "welcome FDA, what took you so long to get here?" If you are not doing what you should be doing, either fix it ASAP or get out of this business because the FDA will be the least of your problems... just wait until the product liability attorneys show up at your door. It’s as simple as that!
Michael Drues Ph.D., President, Vascular Sciences
Attend this speaker's sessions: Why Design Validation is More Than Testing: How do we validate our validation? / Post Market Surveillance: If a Device is FDA Cleared or Approved, or EU CE Marked, is that Device Safe and Effective?
Expert Tip #2
An audit or inspection is something that should be prepared for from Day 1 of your product engineering and development efforts. If good engineering and good management practices are being followed, you will be collecting evidence – product requirements, product design, design review minutes, etc. – from the beginning of your project and will be able to confidently show an auditor or inspector your organization understands and follows design control processes. Certainly, having a good filing and organization system (i.e. QMS) is essential to be able to locate and produce requested material during an audit, but creating the necessary material and evidence of following good engineering and management practices must be done from the beginning and is very difficult to backtrack and produce documentation and evidence after engineering and development has occurred.
Brad Graves, Principal / Project Leader, RND Group
Attend this speaker's session: Strategies for ensuring a Medical Device released under EUA will stay on the market after EUA expires
Expert Tip #3
If you are new and don't have alot of experience with external audits, I would look to bring in an independent resource that can perform a pre-audit of your systems. This will help give you experience answering questions and identify gaps.
Thor Rollins, Director of Toxicology and E&L Consulting, Nelson Labs
Attend this speaker's session: Recent FDA feedback Regarding Extractable and Leachable Testing and How to make sure FDA will accept your testing protocol
Expert Tip #4
The best way to prepare for an external audit or inspection is to make sure you are ready now! Don’t wait until an inspector arrives or an inspection/audit is scheduled! Ensure that your QMS documents are up to date by performing assessments against current regulations, standards and guidance documents; perform internal audits and management reviews at regular intervals; address CAPAs on a regular basis; and ensure that your DHF documents adhere to your procedures and meet current regulations, standards and guidance documents.
Cathy Wilburn, Director of Quality Assurance and Compliance, RND Group
Attend this speaker's session: Strategies for ensuring a Medical Device released under EUA will stay on the market after EUA expires
Expert Tip #5
Prior to the audit, take a field trip to the floor to observe processes. Even though internal auditing and standard work are likely part of your processes, how would a process look to an outsider? What questions might an auditor have about a process? Physically, how does the observation area look? Try to have the perspective of an outsider and determine how you can put your best foot forward.
Jon Speer, Founder & VP of QA/RA, Greenlight Guru
Attend this speaker's session: How to Implement and Maintain an Audit-Ready QMS Leveraging Technology
How can QA/RA professionals get product engineers to be more engaged during the post-market process?
Expert Tip #1
Ask them one question: would you recommend using your device for a family member, friend or yourself? If the answer is yes, you have nothing to worry about. If the answer is no... you better start worrying!
Michael Drues Ph.D., President, Vascular Sciences
Attend this speaker's sessions: Why Design Validation is More Than Testing: How do we validate our validation? / Post Market Surveillance: If a Device is FDA Cleared or Approved, or EU CE Marked, is that Device Safe and Effective?
Expert Tip #2
As a medical device software company, we conduct regular defect review meetings between QA/RA and Engineering – both during active product development times and during post-release times. During these defect review sessions we analyze each defect/issue, determine the technical impact and risk of changes to address the issue, and assign priorities. Our engineers are responsible for implementing fixes and generating new “bug fix” releases, which keeps them engaged. Another aspect of keeping engineers engaged and interested is including product quality as part of performance reviews, with defect counts and responsiveness to addressing defects as primary measures of this performance review item.
Brad Graves, Principal / Project Leader, RND Group
Attend this speaker's session: Strategies for ensuring a Medical Device released under EUA will stay on the market after EUA expires
Expert Tip #3
Educate to increase engagement. Teach product engineers about the post-market process, making sure they understand how, with their specific expertise, their involvement can improve the product and its safety.
Cathy Wilburn, Director of Quality Assurance and Compliance, RND Group
Attend this speaker's session: Strategies for ensuring a Medical Device released under EUA will stay on the market after EUA expires
Expert Tip #4
Unfortunately, engineers often perpetuate several myths about quality. One is that post-market events are not their concern, they’ve done their part and they can move on. To debunk this myth it’s important that engineers understand that quality events are indications of product and process quality--of how well an engineer executed the design and development process.
Jon Speer, Founder & VP of QA/RA, Greenlight Guru
Attend this speaker's session: How to Implement and Maintain an Audit-Ready QMS Leveraging Technology
What other tips, advice or best practices do you want to
share with medical device quality and regulatory leaders?
Expert Tip #1
Meeting the regulatory and quality requirements is the academic equivalent of being a "C" student. Our goal should not be compliance, that's a pretty low place to set the bar. We can and should do better than that!
Michael Drues Ph.D., President, Vascular Sciences
Attend this speaker's sessions: Why Design Validation is More Than Testing: How do we validate our validation? / Post Market Surveillance: If a Device is FDA Cleared or Approved, or EU CE Marked, is that Device Safe and Effective?
Expert Tip #2
Speaking from the perspective of a medical device software developer, I would recommend to always be on the lookout for new tools and technologies that can improve the efficiency of your engineering efforts. This could be a new programming language, taking advantage of new technologies – like cloud computing or open source software, or adopting new methodologies like agile instead of waterfall. The traditional inertia to change is a concern that FDA regulations prevent or discourage new approaches to engineering and development. But, we have found that the guidelines are flexible enough to accommodate new technologies and approaches, as long as you understand the intent of the regulation or guidance and can produce a final product that shows evidence of following good engineering practices.
Brad Graves, Principal / Project Leader, RND Group
Attend this speaker's session: Strategies for ensuring a Medical Device released under EUA will stay on the market after EUA expires
Expert Tip #3
Stay up to date with regulations, standards and guidance documents. Also, hire help where you need specific expertise.
Cathy Wilburn, Director of Quality Assurance and Compliance, RND Group
Attend this speaker's session: Strategies for ensuring a Medical Device released under EUA will stay on the market after EUA expires
Expert Tip #4
Don’t hesitate to seek industry-specific tools and technology that will help ensure quality and compliance. There’s almost always a way to improve a process. Sometimes that requires an engineer to shift their mindset and embrace new tools that allow for the freedom to focus on quality rather than compliance. Ultimately, this shift will lead you back to what you’ve been trying to accomplish in the first place: developing the safest, most effective medical device that improves the quality of life for the patients who use them..
Jon Speer, Founder & VP of QA/RA, Greenlight Guru
Attend this speaker's session: How to Implement and Maintain an Audit-Ready QMS Leveraging Technology
Practical Insights into Managing and Leading Medical Device Companies and Teams During the COVID-19 Pandemic
The medical device industry has the unique opportunity to be the catalyst for change in today's unpredictable climate. Understand how you can create teams to enable remote work, use quality to your advantage to create life-saving devices, and stay on top of what's changing in the industry.
Get your free ticket to attend this track's sessions at The Greenlight Guru True Quality Virtual Summit.
What advice or recommendations would you give to medical device leaders to effectively lead and manage their teams during the pandemic?
Expert Tip #1
Leadership needs to provide regular communication, be transparent about the impact of the pandemic on your company, and set expectations with your team, investors, partners, and customers. There is a great deal of uncertainty in the world, and clarity from management is one of the keys to a healthy organization.
Paul Grand, CEO, MedTech Innovator
Attend this speaker's session: How to Navigate Raising Funds for Medtech Startups During a Pandemic
Expert Tip #2
It is crucial for leaders to recognize that it is difficult to expect their teams to give their absolute best at all times in a state of distress for their family's well-being. Personally, I believe the key purpose of a leader is to continuously motivate and support a team, empowering them to deliver their best work while being absolutely empathetic towards challenges in their life.
During the pandemic and in the months following, it’s imperative that leaders are consistently transparent, communicative, and responsive to their team. It is paramount that we prioritize the work-family balance, as well as the mental and physical health of an employee. Included in arrangements likely to produce effective and efficient work-life structures is showing unwavering trust, supporting flexible working arrangements, and vocalizing empathy when it comes to compounding responsibilities, such as caring for children or elderly family members.
Through consistent communication, leaders not only foster trust but offer a human element that many strive for during periods of involuntary isolation. Leaders may also want to consider planning or organizing virtual team activities that encourage the social connection among the entire team. For instance, a few of the activities that Azzurians regularly participate in are the virtual cooler meetings, pizza parties, and virtual team games that lessen the distance between teammates during this time of self-isolation.
Amishi Vairagade, Team Lead, Consultant, Azzur Group
Attend this speaker's session: Practical Insights into Managing and Leading Medical Device Companies and Teams During the Pandemic
Expert Tip #3
3 things:
1. Remain focused on the fact that this is temporary. The natural instinct may be to slow down and withdraw resources. Instead, this is an excellent time to strategically plan and dedicate time, staff and resources to ensuring that the post-pandemic time capitalises on key changes in healthcare.
2. Over communicate. It is evident that teams that have the most frequent communication and updates succeed. Critical to this is admitting when you don't have information or don't know. Admitting this builds credibility, and lets teams know you are working on things.
3. Be patient and understanding. This has impacted everyone in a unique and slightly different way. Teams will be distracted in very personal ways, and while it is critical to keep your focus on the long term objectives, small distractions and delays are inevitable. The most resilient people and organisations are flexible and adaptable to this.
Attend this speaker's session: The post-COVID Value Shift & How MedTech Companies can Capitalize
Expert Tip #4
Be cognizant of the impact on all stakeholders as a major disruption to workflow, patient flow and utilization is occurring. In large this will be very temporary, in some instances the delivery of care and sites of service will shift in response.
David Uffer, Partner, Alira Health
Attend this speaker's session: How to Navigate Raising Funds for Medtech Startups During a Pandemic
Expert Tip #5
Don't forget your most precious asset - people, people, people. We are all going to face many business challenges in light of the pandemic - but the organizations that holistically consider how they are impacting people, both their patients and their staff and teams, are most likely to effectively navigate these circumstances.
George Zack, Principal & Co-Founder, Two Harbors Consulting
Attend this speaker's session: Remote Audits in a COVID-19 World
Expert Tip #6
The first thing I would say is be sensitive to employees personal situations. You have to run a business obviously but it doesn't mean you can't work with each employee to meet the needs of themselves and their family and still provide what is needed at work. Review goals and when needed realign expectations to match current circumstances.
Todd Hillam, Senior Scientist, Nelson Labs
Attend this speaker's session: What we Learned from the Race to Supply the Market with Respirators, Masks, and other PPE
Expert Tip #7
Communicate often! Let your people know where things stand with the business. Meet a ton via online tools - as it is connection that keeps us all engaged. With everyone at home, each of your workers will be dealing with different issues, both private and professional. The distributed workforce requires even more touch points to help people stay connected.
Dan Purvis, CEO, Velentium
Attend this speaker's session: Responding to the COVID-19 Pandemic: Scaling Up Operations When It Matters Most
Expert Tip #8
Balance your communications. Working remotely brings special challenges that make meetings more difficult, so focus on efficiency in meetings to ensure your team still has time to do their work and manage their situation at home.
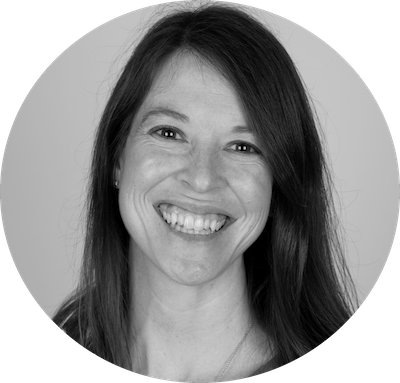
Attend this speaker's session: Why Remote Research Is (or isn't) Right for your project
Expert Tip #9
Stay connected with your team, but understand that remote work life is not the same as office work life. Your team members with a family may be dealing with small kids, noisy pets, and/or bad internet! Being understanding and accommodating will go a long way in getting your team through this crazy time in one piece!
Colton Turner, Sr. Human Factors Specialist, Ph.D Human Factors Psychology, Priority DesignsAttend this speaker's session: Why Remote Research Is (or isn't) Right for your project
Expert Tip #10
I think it's important to maintain communication and flexibility with your during the pandemic. With the majority of employees working from home there are many new issues that can affect productivity for each person. It's important to discuss internally the best way to manage expectations and work together to improve efficiency. Allowing greater flexibility for working hours or days can improve efficiency and reduce the added stress due to the pandemic.
Kyle Rose, President, Rook Quality Systems
Attend this speaker's session: How to get your COVID-19 Related Medical Device to Market Under FDA Emergency Use Authorization (EUA)
Expert Tip #11
I always say that conflict arises from violated expectations. Therefore, manage your expectations as a leader, and be clear about your expectations of your team during these challenging times. The last thing you want to do is have misunderstandings or conflict within your team when working well together/apart is so critical.
Allison Komiyama, Principal Consultant, AcKnowledge Regulatory Strategies
Attend this speaker's session: Digital Health and Remote Monitoring Devices: the Impact of COVID-19 on Their Regulation
Expert Tip #12
We’re in the midst of an unprecedented global health crisis. This crisis calls on the medical device industry to work closely with customers, patients, regulators and public organizations for the sake of public health. The news will be fast-paced, and much of it will be disappointing, frustrating and dispiriting. The key, however, will be for leaders to focus on how they can make the most effective contributions to control the spread of the virus and save lives. Short term, that might mean ramping up production to new levels; long term, that might mean sticking closely to regulatory guidance to ensure that speed doesn’t destroy quality, creating even more problems in the future. Leaders must communicate to their organization the essential role that the med device industry has in the fight against COVID-19.
Jon Speer, Founder & VP of QA/RA, Greenlight Guru
What advice or actionable takeaways from COVID-19 would you give medical device leaders to prepare their organization for future disruptions?
Expert Tip #1
The impact of this pandemic will be long lasting. Take the time to strategize about scenarios where things get better, stay the same, or get worse. Do what is necessary to prepare your organization for survival in any of those scenarios and to be able to quickly take advantage of new opportunities. You need to be super prepared and super nimble.
Paul Grand, CEO, MedTech Innovator
Attend this speaker's session: How to Navigate Raising Funds for Medtech Startups During a Pandemic
Expert Tip #2
Remote working is here to stay, so companies need to plan strategically and prepare their organization accordingly.
An effective leader customizes and leverages a company's employee assistance program resources, as well as puts into place comprehensive training specific to employees’ mental, physical, and emotional preparation for the “new” work-life balance.
For starters, there are a plethora of online platforms that offer mindfulness and wellness programs (by trained professionals) that focus on coping with anxiety/stress and fosters overall well-being. Another training which can be established by leaders is to build and strengthen virtual collaboration and communication within the teams. Let’s face it: with most meetings held virtually, it is more challenging to negotiate and resolve issues with significantly less body language.
Next, investing more in IT would be a smart move. Per the Gallup Organization (Gallup.com), one of the keys to an engaged workforce is that they "have the materials and equipment" needed to do their job right. With all of us working remotely, there are manifold more issues around getting video tools working properly so that remote limitations are minimized.
Lastly, leaders must evaluate and formulate robust pandemic response action plans for any future disruptions by incorporating the recommendations, expertise, and protection interventions recommended by regional, state, and national organization authorities.
Amishi Vairagade, Team Lead, Consultant, Azzur Group
Attend this speaker's session: Practical Insights into Managing and Leading Medical Device Companies and Teams During the Pandemic
Expert Tip #3
Have a pandemic preparedness plan and a general existential threat plan. In a pandemic, the healthcare ecosystem needs to focus on the Staff (healthcare workers), Stuff (devices, drugs and diagnostics), Space (working space and healthcare facilities), and systems (ensuring operating plans and policies adapt). Having contingency plans in place for each of these now, can avoid disruption in the future. The device companies that understand how these are intricately linked, and can adapt quickly will succeed. This success will translate to both organisational and system level. We need to learn from this pandemic in a far more collaborative way than we did for SARS or MERS. During these outbreaks having the staff, stuff, space and systems was NOT learned from as well as it should have been. This needs to be avoided.
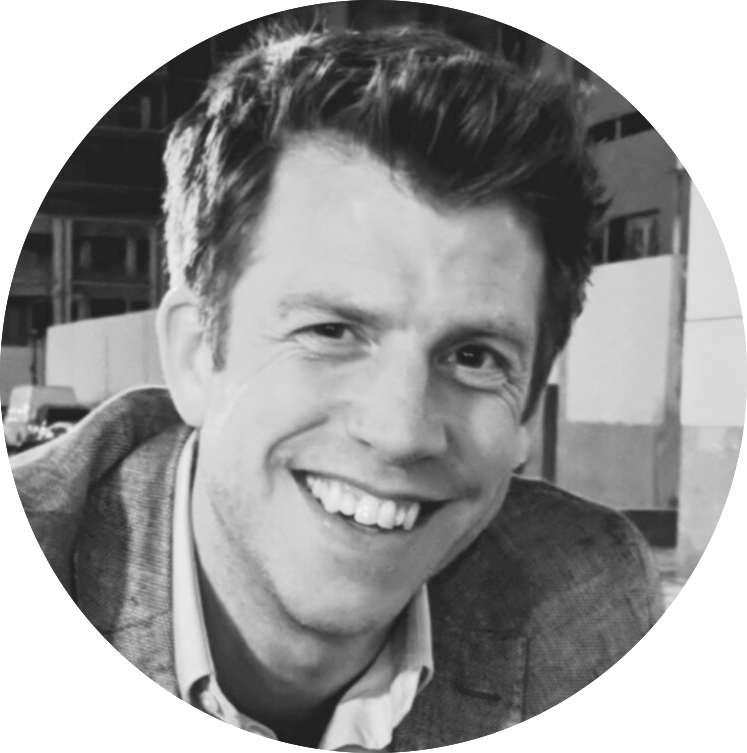
Attend this speaker's session: The post-COVID Value Shift & How MedTech Companies can Capitalize
Expert Tip #4
Maintain funding to ensure ongoing operations with larger reserves that typically projected in the past, disruptions cause inefficiencies and utilize more resources.
Attend this speaker's session: How to Navigate Raising Funds for Medtech Startups During a Pandemic
Expert Tip #5
1. Re-evaluate your supply chain - all of it.
2. Re-consider true continuity in your business plans. Many have been involved in product risk when dealing with medical devices Consider the entirety of your QMS and business in a similar fashion - what is the risk if I can't do this or I have to do it under compromised circumstances - what is the mitigation you will undertake for any business process?
3. Consider truly what work needs to be done "face to face" and what can be done "virtually" or using on-line tools so you can be clear in delineating those.
George Zack, Principal & Co-Founder, Two Harbors Consulting
Attend this speaker's session: Remote Audits in a COVID-19 World
Expert Tip #6
Make sure you have contingency plans in place for alternative work schedules and location (work from home). Take a look at how quickly you are able to shift the work flow or your employees to different tasks or departments than they are actively working.
Todd Hillam, Senior Scientist, Nelson Labs
Attend this speaker's session: What we Learned from the Race to Supply the Market with Respirators, Masks, and other PPE
Expert Tip #7
Ask "why not us?" In the event of a global situation, the solution to the crises is built on thousands of leaders stepping into and filling the gap that their organization is uniquely positioned to address. But that takes courage - and a culture throughout the organization that assures your bold move will be followed by your team. Build that culture now so you are ready when the need arises.
Dan Purvis, CEO, Velentium
Attend this speaker's session: Responding to the COVID-19 Pandemic: Scaling Up Operations When It Matters Most
Expert Tip #8
This pandemic has taught us to ramp up quickly on what technology can do for us. We've learned a lot about what it can provide us in lieu of our typical face to face communications, so focusing hard on how to continue to leverage it and keep up on what's available to maintain these efficiencies in the future can help us work faster and smarter, even once we're back to business as usual. That way, maybe the learning curve isn't so steep next time.
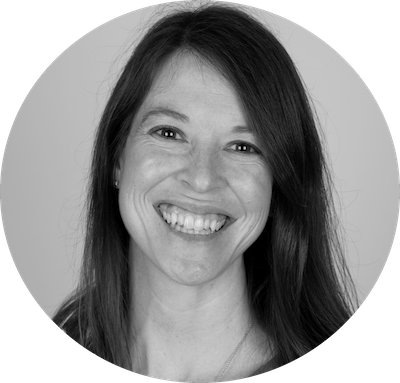
Attend this speaker's session: Why Remote Research Is (or isn't) Right for your Project
Expert Tip #9
From a human factors research perspective, it is important to stay flexible with the research methods you use. But with that flexibility comes the need to understand where you can afford to bend without breaking. Just because you can't conduct research the way you always have doesn't mean you can't conduct research at all, and just because you can conduct research a different way doesn't mean you should. Understanding the pros and cons of each method and their overall ability to contribute to your research goal is critical to conducting meaningful and useful research.
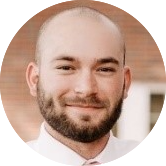
Attend this speaker's session: Why Remote Research Is (or isn't) Right for your Project
Expert Tip #10
I think this pandemic really reinforces how critical the need for quality practices throughout your company and supply chain really is. The demand for medical devices and related items for COVID-19 has shown that a lack of quality can directly impact the front-line workers using these tools. Maintaining a strong emphasis on quality from early design control through post-market surveillance is critical for all device companies now more than ever.
Kyle Rose, President, Rook Quality Systems
Attend this speaker's session: How to get your COVID-19 Related Medical Device to Market Under FDA Emergency Use Authorization (EUA)
Expert Tip #11
Be flexible and willing to change course if/when regulations are revised. This means having a team that works well together along with a quality system that isn't overly burdensome. If you can be part of the solution for a national or global emergency, that will benefit more than just your company.
Allison Komiyama, Principal Consultant, AcKnowledge Regulatory Strategies
Attend this speaker's session: Digital Health and Remote Monitoring Devices: the Impact of COVID-19 on Their Regulation
Expert Tip #12
Leaders must plan against the downstream effects of pandemic disruptions. You must consider the impacts on areas such as clinical trials, patient travel and the impact social distancing will have on your team if working remotely. Quality needs to remain at the center of operations and paper-based systems will no longer be manageable in ensuring quality and preparedness for future disruptions. Success lies in using industry-specific tools that will centralize your entire document management flow into a single cloud-based system, with permissions that you can tune to your team and security that keeps your data safe.
Jon Speer, Founder & VP of QA/RA, Greenlight Guru
For complete event details of The Greenlight Guru True Quality Virtual Summit, including the full schedule and lineup of speakers, visit https://virtual-summit.greenlight.guru/ or click the button below to register for free.
Jon Speer is a medical device expert with over 20 years of industry experience. Jon knows the best medical device companies in the world use quality as an accelerator. That's why he created Greenlight Guru to help companies move beyond compliance to True Quality.