Switching to an Electronic Device History Record (eDHR): What Medical Device Companies Should Know
Your device history record (DHR) is one of the final forms of documentation you’ll need before your product ships. That doesn’t mean it’s an afterthought, however.
The DHR is a crucial component of your quality system because it ensures that the products you’ve manufactured meet all your specifications and that each batch, lot, or unit can be quickly identified.
In the past, device history records were commonly compiled using manual, paper-based systems. However, as you’ll soon see, these paper systems are becoming a thing of the past (and that’s a good thing!).
They’re being replaced by electronic device history records (eDHRs), and in this article, I’m going to break down the differences between the two and explain why it’s probably time to make the switch to an eDHR.
What is an eDHR?
Before we get into electronic device history records, it’s important to establish exactly what the traditional DHR does.
The DHR lives in your QMS and it serves as a final check on the products you’re manufacturing, ensuring that each batch of medical devices meets the specifications in your device master record (DMR).
Remember, the DMR contains everything you need to know to build and test your device. Your DHR is a record of everything you did to make the device. However, you may actually end up with many DHRs because FDA requires them for each product batch.
The term “eDHR” may seem to imply that it’s simply an electronic version of a traditional DHR. But that’s not entirely correct. Many companies use electronic tools like Excel to manage their device history records, but still print them off as part of their paper-based QMS.
An eDHR is a paperless, electronic system that captures all information associated with the production of a medical device and facilitates production processes. An eDHR is also distinguished by the fact that it often lives within a larger system—like an eQMS—that ensures it is connected to other quality processes and data is not siloed.
What information should be included in your eDHR?
FDA clearly sets out the information your eDHR must include in CFR 21 Part 820.14:
Each manufacturer shall maintain device history records (DHR's). Each manufacturer shall establish and maintain procedures to ensure that DHR's for each batch, lot, or unit are maintained to demonstrate that the device is manufactured in accordance with the DMR and the requirements of this part. The DHR shall include, or refer to the location of, the following information:
(a) The dates of manufacture;
(b) The quantity manufactured;
(c) The quantity released for distribution;
(d) The acceptance records which demonstrate the device is manufactured in accordance with the DMR;
(e) The primary identification label and labeling used for each production unit; and
(f) Any unique device identifier (UDI) or universal product code (UPC), and any other device identification(s) and control number(s) used.
The fact that the DHR is given its own section in Part 820 should tip you off to just how important your process for creating DHRs is to FDA inspectors.
Why use an eDHR instead of paper?
The real value of an eDHR is not that you can see it on a laptop instead of in a binder. The value lies in its connections to the rest of your QMS. This leads to a number of compounding benefits that simply can’t be realized with a paper-based DHR:
-
Everything in one place. Paper-based systems are by their nature disconnected. Data is often duplicated, siloed, or simply difficult to find. On top of that, manual DHRs aren’t connected to other quality processes within a QMS, making it difficult to understand how various data—like complaints, nonconformances, and production information—are correlated. An eDHR, on the other hand, is integrated with the rest of your QMS, ensuring that critical data is shared, offering you a more holistic view of the inputs to your DHRs.
-
Streamlined processes. If you’ve used a paper DHR before, then you know the processes for compiling the necessary information are generally slow and error-prone. An eDHR can streamline your processes by automating tasks like data collection and review. It also offers increased visibility into your DHR process, helping you identify and relieve any bottlenecks.
-
Fewer quality and compliance risks. There’s no way to put it gently: paper DHRs leave you less prepared for an FDA inspection. The last thing you want during one of these already high-stress events is to be frantically looking through a list of PDFs, spreadsheets, or even filing cabinets to find the records you need. An eDHR ensures that not only can you easily find the documents you need, but you can rest easy knowing they’ll be the most up-to-date version available.
Paper DHRs are inherently limiting. Some companies can get away with using them initially, but there will always come a time when it makes more sense to switch to an electronic system to manage your eDHR.
Ensure all device data, files, and records are up to date and easy to find with Greenlight Guru
An eDHR is a critical component of manufacturing safe and effective medical devices, as well as being ready for FDA inspections at any time. However, it’s just one component of what should be an automated, integrated, and fully traceable QMS.
At Greenlight Guru, our QMS software was built by medical device professionals, for medical device professionals. That means you have a secure, cloud-based solution that houses all your critical documents and serves as a single source of truth. So when you use Greenlight Guru Quality, you can rest assured that your eDHR is connected to the rest of your quality system, giving you seamless visibility and traceability.
Stay audit-ready and fully compliant. Get your free demo of Greenlight Guru today.
Looking for a design control solution to help you bring safer medical devices to market faster with less risk? Click here to take a quick tour of Greenlight Guru's Medical Device QMS software
Tom Rish is a Medical Device Guru at Greenlight Guru who works with customers to utilize their QMS software to build safer products on expedited timelines. He is a Biomedical Engineer who began his career developing implant and instrument systems in the orthopedic industry. He enjoys helping customers successfully...
Related Posts
Computer Software Assurance for Medical Devices: What Does FDA’s Draft Guidance Mean for You?
Medical Device 3D Printing: Should You Make the Move?
What is the True Cost of Poor Quality for Your Medical Device Company? (Free Infographic)
Get your free resource
Benefits of a Formal Document Management System
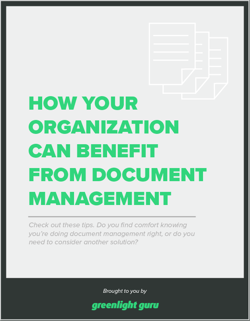